Advanced automation is the future for flexo platemaking growth
In the past 20 years, technology has changed the nature of flexo platemaking.
31 Mar 2017 | By PrintWeek India
In the old days, flexo plates were all processed with basic electromechanical equipment. When, later, electronics penetrated the industry, flexo platemaking equipment also took advantage of it. Control systems were introduced to regulate processes and reduce the need for human intervention. Embryonic forms of automation started and flexo platemaking equipment became slightly more sophisticated.
Now that computers, software, connectivity and technology have developed further, advanced robotic automation has set new standards for the industry. Advanced and fully automated flexo plate processing lines have been introduced enabling flexographers to produce plates at outstanding speeds and with great repeatability and quality. Advanced robotic automation in the Flexo Platemaking industry is the process of integrating processing equipment to automatically perform a variety of applications such as imaging, exposing, punching, washing-out, drying, finishing, plate handling, storing, etc, all in one go.
Advanced robotic automation in full processing lines has become the competitive advantage in today’s flexo platemaking world and the determining factor in whether a company will remain competitive within the flexo platemaking industry. Some call it the “fourth industrial revolution."
Regardless of what you call it, the numbers are proof that robotic automation has been exponentially incorporated into Tradeshops and Converters; bringing incredible precision, productivity, and flexibility. Additionally, we are now seeing a boom in advanced robotic automation that is able to seamlessly work hand-in-hand with human workers to further increase flexibility and efficiency. What we see is the Flexo Platemaking Internet of Things on the rise.
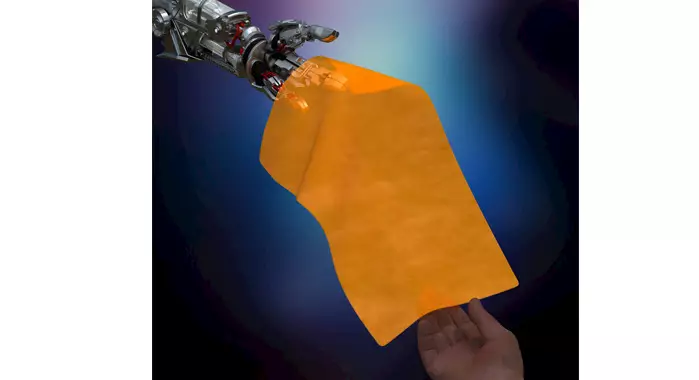
Advanced Robotic Automation is able to seamlessly work hand-in-hand with humans
Globally, it is estimated that about 500 fully automated Flexo Platemaking lines will be installed before the end of 2020. The global market value for fully automated Flexo Platemaking lines is estimated around 500 million US dollars.
While advance robotic automation has become a resource for remaining competitive in the flexo platemaking industry, there are definitely some factors to be considered in order to be competitive and to get a decent return on investment (ROI).
Depending on the operations, advanced robotic automation may or may not be a good fit.
On the other hand, if the operation has a larger facility with several operators on the shop floor to process medium to large quantities of plates per day, advanced automated lines would be better suited. Low mix/high volume and high mix/low volume runs, are another discriminating factor as advanced automated processing lines grant the flexibility needed to get the job done.
Understanding the initial investment
The initial investment to integrating a fully automated Flexo Platemaking line of the newest generation into your business can be significant. The cost of advanced robotic automation should be calculated in light of a conspicuous financial budget.
Fortunately, there is at least one Flexo Processing equipment manufacturer that understood the Flexographers dilemma and started developing a family of units that can be combined to build a complete and fully automated robotic line not just as a monolithic solution, but also over a period time, even several years.
That solution, is known as modular robotic system and is characterized by “standard” functional units equipped with built-in interfaces that can be joint together to build automated systems in different configurations, by simply upgrading the software.
Modularity offers great flexibility in design. The ability of adding new units by merely plugging in a new module helps overcome fast increasing customer demands and makes the manufacturing process more adaptive to change.
If you are considering rejuvenating your plate processing line, or parts of it, collaborating with a specialized integrator may save you considerable time and money. Using the integrator’s expertise to discuss your plate processing system, the raw plates you are using and your expectations, is a nice first step; it can help you take the right decisions.
Understanding the advantages
The main advantages of simple automation are obvious and therefore clear to anyone. For example, every time you need to process a plate your plate processor automatically defines the wash-out parameters, saving time that you would have previously spent.
Advanced robotic automation takes that one step forward, linking all the units and plate processing phases to each other by bridging the machines and making them communicate. With classical configurations operators spend hours a day doing small tasks like reconfiguring the processing equipment (exposure, wash-out, dryer, etc.) and transporting the pales from one unit to the next, wasting a considerable amount of time. Automating those tasks allows flexographers to work on what they truly consider most important.
Having a plate processing system that is fully automated speeds up the production time. Since no thinking is required by the machine, there is better repeatability, and less human error. When a fully automated robotic line is programmed to perform a task over and over again, the accuracy and repeatability compared to that of an employee is far greater.
No one is perfect, and we are all prone to making mistakes. Which is why a machine that performs repeated tasks is less likely to make mistakes than any operator. Adding a fully automated robotic plate processing system to a production site, means that less employees and lower skills are needed to get the job done. It also indicates less safety issues, which leads to financial savings.
With having less employees and lower skills required, there are numerous costs that are reduced such as payroll, benefits, sick days, etcetera. Having automated systems means having less human intervention, i.e. operators who perform tasks that can be dangerous and prone to injury, which can make the work environment safer.
A lean manufacturing system is crucial for increasing efficiency. Advance robotic automated lines can work longer and faster which increases production rate while being so accurate that the amount of raw material used can be reduced, decreasing costs on waste.
By decreasing the footprint of a work area by combining parts of your production line, you can utilize the floor space for other operations and make the process flow more efficient.
Investing in advanced robotic automated equipment creates a valuable resource for low mix/high volume and high mix/low volume, which in turn, will attracts customers and increase profitability.
In essence, the advantage can be summarized as follow:
• Reduction in Plate Processing Cycle Time
• Increase in accuracy and repeatability
• No human error
• Less employee costs
• Increased safety
• Higher volume production
• Decrease in costs on waste
• Reduce Production Cost
• Better Floor Space Utilization
• Stay Competitive
Flexographers should ask themselves how they could benefit from Advanced Robotic Automation. What do they spend their time doing that they could automate to free-up some time that could be spent doing something worthwhile?
After getting one task automated, flexographers will find others that should be automate too. Having many time consuming tasks automated will really affect the bandwidth of the organization has.
Let technology do basic and repetitive things while your organization gets on with the things that are truly important for the business.
About the author
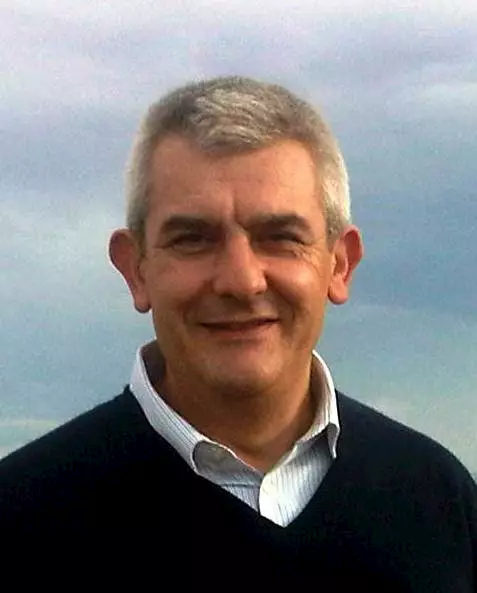
Pier Luigi Sassanelli (SASS) is an experienced Marketer with wide international experience in consolidated and emerging economies. Talented to identify business opportunities and translate them into profitable growth, he is currently a Strategy Advisor for several Global and Regional companies operating in Food and Packaging Printing. Before, Sass was with DuPont for 30 years. Lately he worked for DuPont Nutrition & Health as Strategic Marketing & Innovation Process Leader and for the DuPont Corporation where he co-designed the renowned DuPont Marketing Excellence program and co-founded the global DuPont Marketing Academy. Prior to that he was Marketing Manager, Global Marketing Communications Manager and Global Equipment Business Manager for Cyrel.