[Advertorial] Basics of die-cutting
One of the defining steps in making a perfect carton is die-cutting. But apart from choosing a right die, how can you achieve highest efficiencies and at the same time minimise makeready times? Mukul Luthra of Artize Die Makers dwells on key steps of the operation
04 Jun 2018 | By PrintWeek India
Don't cut multiple sheets in a single impression. One sheet at a time earns best results.
Do use different creasing matrix "channel width" with the grain and cross-grain directions.
Do have a right combination of ejection material on the die. Different areas on the die require different "cutting force", which calls for a correct combination of height and hardness of rubber.

➊ Open cell rubberDo have a right combination of ejection material on the die. Different areas on the die require different "cutting force", which calls for a correct combination of height and hardness of rubber.
➋ Vulcan rubber
➌ C-profile rubber
Do keep balancing knives in a calculated way such that the cutting die is balanced on the platen leading to less makeready time and better performance of platen press.

Do measure the substrate caliper and use it for calculating and choosing the right creasing matrix size (depth x width) and creasing rule height.
Don't use scrap rubber as ejection material. As the scrap rubber is not consistent in height and hardness, it can cause pressure issues and result in long makeready time.
Don't use 5mm cutting plate. It is not possible to retain the channels as they have to be cleared for the next job. It leads to increase in makeready time and cost as every job entails a new makeready.
Do level the whole platen by using zonal makeready procedure. This will help in even die balancing and consequent defect-free cutting.
Do fresh make-ready again when you have shim/patching tape all over a large portion of a die.
Do fresh make-ready again when you have shim/patching tape all over a large portion of a die.
Don't use substrate grammage (gsm) for reference. Instead use substrate caliper.
Don't paste foiling and embossing dies on the platen with liquid adhesive. There are better solutions available in the market like toggles or heat tape.

Do use 4+1 mm plate for makeready, it saves time and energy since the makeready can be retained for each job on the 1mm plate.

Don't put full pressure on the first punch. It can damage the cutting rules. Instead get trained to use the "zero pressure makeready procedure".
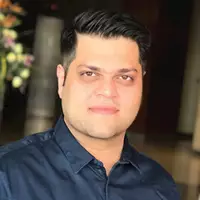
Mukul Luthra is a founding partner at Artize Die Makers, a specialist manufacturer of laser dies
