ATM in Daman inks high growth
Five years ago, Saill set up the first ink ATM in the country. Today, they distribute 150 tons of ink per month to 700 customers, as Ramu Ramanathan finds out.
01 Oct 2010 | By Ramu Ramanathan
Rajkumar Lodha, who heads Saill, states: "Our company has a market share of 65%." In real terms this is translated into 150 tons of liquid, base and process inks per month.
Ink dispenser supplies 150-tons of ink per month
The science of colour matching
Micro Inks has its factories in the same neighbourhood, And yet, Saill scores. This is because of its ability to customise delivery up to five kilos and even a single kilo. This reduces wastage and customers do not have to stock ink.
Additionally, if a customer asks for a colour match, Saill can provide it within hours. Lodha explains, "The selection of colourants and tinting to shade of a printing ink is time consuming." This means the exact procedure used in colour matching of printing inks will depend on the exact nature of the work and the skill and experience of the colour matcher.
Lodha explains: "The type of ink, the process, initial and anticipated order quantities are vital pieces of information required by our laboratory incharge." The Saill team archives the data about the details of the press and range of subsrates.
Lodha says: "Ink is the tiniest component in the print workflow, but we have to be very careful. For example: if the ink is required for food packaging then the ink should have properties such as odour and rub resistance. Also it should be suitable for deep freezing. Plus it should adhere to health norms."
It doesn't stop there. During the post-printing process, if many processes are involved, their effect is taken into account. Lodha adds: "Over-printing, waxing, heat-sealing, laminating and embossing can have a bad effect if unsuitable materials are selected for the ink formulation."
Ink kitchen provides a quick colour match
Wide range of customers
At Saill, inks are matched by mixing concentrates which are already blended in a suitable varnish in the form of finished inks, or pastes with high pigment loadings. Lodha says: "The market is diverse. Daman, Silvassa and Vapi boast of large scale gravure units (Paper Products, Zaveri, Kris Flexipack, Uniglobe); CI Flexo units (Mehta, Glory Polyfilm, RM Seal), offset units (Parksons Packaging, Borkar, TCPL, Temple, Orient) and screen units (Jolly, Goldstar, Hitech, Clear MyPack, 3-D)."
Saill has 700 customers. But liquid ink dominates with 25 customers accounting for 50% of the company's turnover. Lodha says: "Very fluid, solvent-based inks are used to print in gravure or CI flexo." These inks dry by evaporation, leaving a dry film of resin and pigment on the substrate. The advantage of the process is rapid drying can be obtained on non-absorbent materials such as plastic films and metal foils.
Lodha says: "With solvents, viscosity control is the key." If the viscosity is too high, the the cell-wall pattern will be evident in the shadow tones and the print product will lack smoothness. And if the viscosity is too low, then bleeding will occur which shall entail spreading of the image from the shadow areas.
SAP and more
Saill has implemented SAP. It may sound surprising but Lodha says: "SAP has empowered our productivity."
Clearly, Lodha is a man on the move. He hosts annual events which are attended by the who's who of the print community in the region. He educates his customers. He plans to add a new location to his solvent operation.
Lodha concludes: "This is one of the fastest-growing print regions in India. I want to ensure modern operations with significant capacity reserves, as well as ensuring uninterrupted supply at competitive price levels."
R LODHA: AT A GLANCE
When you see a print job, what do you look for?
I examine the printing ink. And I’m happy if it is Micro Inks.
Best printing process according to you?
CI Flexo because of its clarity and production speed. I think CI flexo will set the pace for the future of the industry.
The best print job, you have seen?
Glucose Parle G biscuit wrapper. They haven’t changed the branding for decades. Plus I love the taste of the biscuits.
The craziest deadline you’ve encountered at your ATM?
It was a job for Pfizer. They required a polypack with buff colour. It was a big challenge to reproduce the exact shade. You need the right chemistry and resins.
Your favourite ink raw material?
The concentrates which are supplied by Micro Inks for all categories of inks. They are so easy to work with.
The best thing about printing inks?
Printing ink runs in my veins. That’s why I say my blood is red. Instead of red blood corpuscles, my blood has organic pigments which are used for process-colour printing because they form transparent films. I joke that pigments like red lake C and toluidine red make my blood look good.
The worst thing about printing inks?
There is a vast variety of variables from polyester to poly inks to deep freeze inks. Everyday newer combinations are being invented and therefore newer print applications like plastic bags, covers, boxes, cartons etc. Today in Daman, Silvassa and Vapi, print firms are printing on BOPP and PVC films, producing advertising materials, promotional flyers, brochures and paper bags.
One advise for your offset customers?
Set the ink and dampening balance correctly, and check on it continuously throughout the printing process. In case of emulsified ink, wash the rollers.
A world without printing inks?
It would be colourless. I cannot imagine such a world.
How do you begin your day?
At 5.45 am I do some brisk walking. This is followed by a heavy workout at the gym. I’ve a controlled diet. This is good for my health.
For you printing ink is ...
Like chutney. Without it, the food is very bland and too much of it can cause damage the next day.
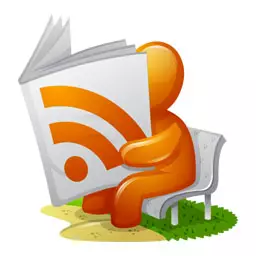
Subscribe to RSS feeds
for the latest news
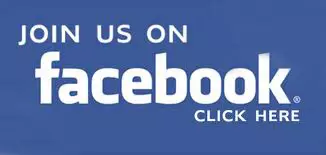
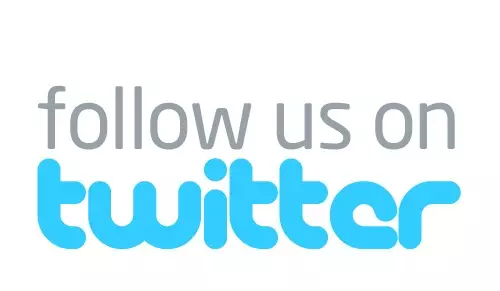