USA-based register control system leader QuadTech shifted base from Ahmedabad to Gandhinagar. This move not just explains the company’s growth, it also signals a new business strategy, Hemant Desai, general manager, QuadTech India tells Noel D’Cunha
Your new plant in Gandhinagar?
Hemant Desai (HD): It’s been in the planning for the past four-five years, discussing how best we can serve the Asia region, what all we can do, and how do we go about it. At the same time, we were facing space crunch in the previous location at Ahmedabad.
It is in this context that we planned our move, not only move the office but also making provisions of a step-by-step scaling of our activities like repairing, assembly, sub-assembly, local sourcing and local billing, in future.
The idea was to import most of the sub-assemblies from the headquarters in US, configure and assemble it as per the requirement, and ship it with local billing.
We opted for an industrial area as a factory unit, rather than shifting the office to a business complex and then to an industrial area should one or more activities require such a move. Our aim was to have everything under one roof, not keep moving from one place to another.
We scraped the existing structure on the plot and built a new one according to our requirements.
Manufacturing in Ahmedabad?
HD: Register controls for packaging, newspaper and commercial printing are our prime and hot products. So from a manufacturing point of view, it will be register controls.
Our products beyond the register controls are the colour solutions, where we have different hardware and software products. The software requires support in terms of training. Here manufacturing per restricted to the configuration, with the hardware being imported and sold through the dealer network. These activities will be carried from here.
Manufacturing of register controls will be our first target.
So it will be more of an assembly plant?
HD: QuadTech has a manufacturing plant in the USA, and the only one. Until now, the India office was more of a sales and service support. We quote, negotiate, and once the deal is finalised, the customer places the order with the headquarters, from where the product is shipped. The customer clears the consignment. We only install and commission the system and provide ongoing service support. That was our role. Now, we are going to import the parts, sub-assembly it, configure the system, assembly test and ship it to our customer with local billing.
What are the benefits for the customer?
HD: We are looking at an angle from where we can reduce the price through local sourcing of certain parts (customising to local requirement). Besides, some of our customers, particularly in the packaging segment, had issues with the import of our products, as well as payment. They wanted a system in place which will allow payment in local currency.
The press manufacturers, who are also our customers, did not have the issue with currency, but with the fluctuation of the dollar rates, particularly the gap between finalising and placing the order.
Both the issues will be sorted out through local billing. Also delivery time. Right now it is around six to eight weeks. Through local assembly, we will be able to keep a stock of the register controls.
Will R&D be part of your activities here?
HD: Yes, development will be the first phase. Two things: one, development of the existing system, particularly, for the local requirements. Of course, this will be in conjunction with our headquarters. Second is to contribute/support the USA development team for new product developments.
Since QuadTech has only one office in Gandhinagar, how do you manage the activities?
HD: QuadTech India started with just two employees in 1993. Later, in 1997, newspaper industry boomed with the advent of colour printing, after which we tied up with Manugraph, packaging customers and packaging press manufacturers. Technical support was the main motive of this office. After the OEM business was started, business in India increased by 30-40% every year. Then slowly our technical support team members increased. There was a need for increasing the sales, so a sales and accounts teams were added. We started stocking spare parts of around Rs three-crore and provided local customers with the spare parts.
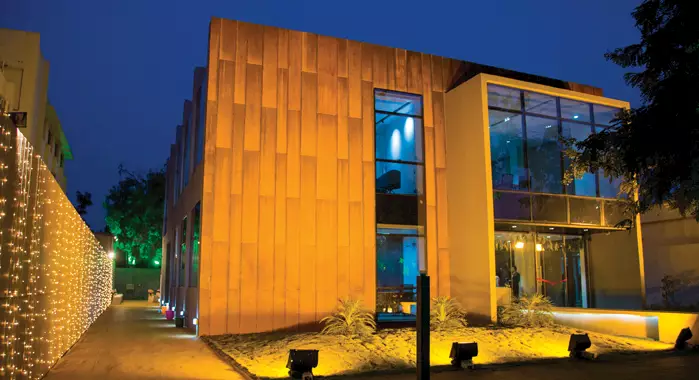
QuadTech India has relocated to a larger, modern facility located in Gandhinagar, Gujarat
In the newspaper industry, printing occurs in the night, from around 11 pm to 3 am. So, if any problem occurs you have to be present instantly. So, to meet these demands, we started our technical support with engineers at different locations in India. Now, we have our engineers in Mumbai, Ahmadabad, New Delhi, Chennai and looking to reach other locations too.
Six to seven years ago, QuadTech had undergone infrastructural changes worldwide. Due to the boost in the Indian market, there was a need for development in the Middle-east and Africa zone. A lot of workforces was outsourced from India. Due to the growth in the technical team, there was a need for sales team also. We have four sales managers based at Ahmadabad, Chennai and New Delhi.
How many QuadTech systems are in India?
HD: In newspapers, we have around 350-400 systems (1,500 or more towers/ webs, 4500 or more cameras). In the commercial, we have 35-40 systems and in flexible packaging over 450 systems.
What are the components that form the register control system?
HD: Firstly, the sensor and cameras are mounted on the press. Presses run at a very high speed and register cannot be tracked manually. The camera tracks the predetermined marks on the web, which are responsible for maintaining the registration. Camera compares the predetermined marks and the inspected marks on the webs to check if there is any displacement of the colours. Then the server receives the input from the camera and the press speed. The server computes which colour has moved in which direction. The server also has a good copy image, and by comparing it guides the web to the desired direction.
What is the accuracy of the systems? After positioning of the web by the system, how consistent is the performance?
HD: Cameras and sensors are capable of identifying the error up to 0.01mm and maintaining the accuracy can be up to 0.02mm. There are many factors that lead to registration or mis-registration. Software (algorithm) is the brain of the system. The algorithm depends on the press it is running on and also on the substrates that are used. It also has the ability to learn the behaviour and make changes accordingly.
Two important things to be considered while considering the consistency: One is to reduce the startup wastage, which is the primary concern. It is very vital to bring the marks within the register as soon as possible. Our camera has the ability to find the marks on the print and track them for registration. Everything is done automatically; involvement of the operator is not required. Once the copy is in the register, now the role of the register control is to maintain that position consistently. Ideally, there should not be any variation in the web. But web passes through dryers, the difference in web-tension, inks and other parameters result in the deviation of the web.
Another reason for mis-registration is acceleration/deceleration. Slicing also imparts variation in the web movement.
What advice would you give while installing a register control system?
HD: Nowadays, there are not much of guidelines required that we need to tell the customers. During the period 1986-1996, there was a need to educate the customers. Colour register control can make a good press to a better press but it won’t make any change to a bad press. Course control has to be better in order to control the finer details. You have to control the web tension first, in order to control the registration.
Smarter presses are coming in the market, what is the role of register control systems?
HD: The role of register control is getting minimised but at the same many features are being added to the inspection system which is not available in the presses. Earlier, makereadies would consume three to four web lengths to achieve registration. Our system has reduced it to two. Even though the presses have become smarter, but it cannot run without inspection systems.
More the press speed, difficult it is to handle the deviation by human force, so we need auto-registration.
Why do you need controls on the web and not on sheetfed?
HD: Compared to the web, only a piece of paper is moving. Once the registration is done, there would be no problem. Level of difficulty in registration compared to the web is very less in sheetfed. In sheetfed, you can stop the press and make the changes, and run the machine again. Whereas when you stop and start the web press again, there is wastage of around 200-300 metres. Along with press becoming smarter, control systems are also becoming smarter. Consider this: your machine is running at 100m/min and you increase it 200m/min, so the time under dryer reduces to half. In order to achieve proper drying, the temperature has to be increased which results in loosening of the web. It is where the web tension control and register controls come into play.
How do registration control and colour management relate to each other?
HD: They complement each other since both are in the press. When we were doing the registration installations, another major problem that came was in colour. Earlier brand owners' demand was only on registration, now they also want exact colour.
What does QuadTech do in colour management?
HD: By making use of the spectrophotometric camera, we do offline and online solution. In offline solution, the operator manually checks the substrate’s LAB value using spectrometer with the desired value and does the required changes in the press. The same procedure is carried out in the online solution. The camera measures the substrate’s colour values, compares it with the good copy and makes changes in the press as required.
What is the importance having both – register control as well as the colour control?
HD: Once the press is running, you want to achieve accurate and sharp print with particular shades at different points. The operator manually changes the ink key settings to achieve the required colour shades and get the accurate and sharp print. The colour parameter when done manually depends on person to person. By using our both system, there is zero percent human interference, resulting in reduced makeready time and wastage. The operator can never achieve zero percent error, whereas it is possible by using our controls. Also, operator corrections depend on the ambiance light, which will vary colour corrections. In our spectrophotometer, we have temperature controlled LED light. With colour control, we not only reduce the consumption of ink but also wastage.
Tell us about ColorTrack.
HD: ColorTrack is for flexible. It is not just a camera but a complete workflow. Printers can get input for the print requirement in many forms like draw-down samples, physical samples, ISO standards, etc. ColorTrack fits in all the departments. Conventionally, after receiving a job, colours are decided and they are made in the ink kitchens separately and then brought into the press. In this process, there are chances of samples losing its actual colour. When it is related to software, everything is defined. In the ink kitchen, software is used for making the inks. It can calculate the amount of ink required for the job and from the ink formulation or the kitchen software, information is sent into the press. When there is some colour variation, the software provides the required amount of change to be done to every press unit. The human interface is eliminated at this stage. In our first print run, the software will check and raise the alarm if it out of tolerance. The software also provides inputs if there is some problem in the viscosity, drying temperature as well as what corrections need to be done. On conventional job set up, there are about four to eight press stops to attain the perfect colour, whereas in ColorTrack it is guaranteed that it will be one print stop. After the first run, LAB value reduces to half. Since the normal delta requirement is around +1 to +2, so after first print, the desired delta value is achieved.
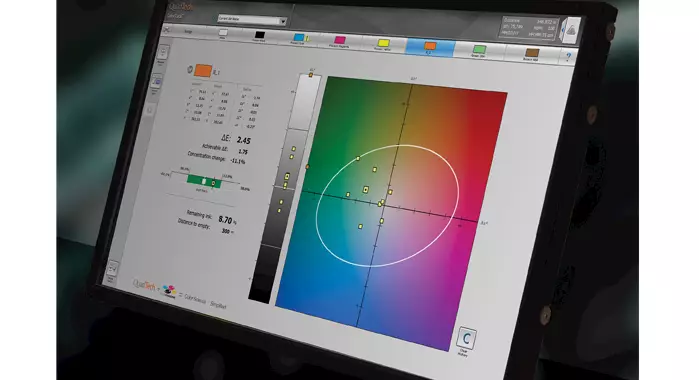
ColorTrack facilitates fast correction of ink formulations at the press
What changes are you seeing in the newspaper and packaging industry?
HD: Presses are becoming smarter and smarter. The speed of the presses has increased. Innovations are on the rise like double folds, centre image advertising in newspapers etc. Colour quality of the newspaper has improved. In packaging, brand owners are demanding colour quality and perfection even as the science of producing perfect colour is growing more complex. Advanced automation is no longer a “nice to have” option. It has become a necessity for print operations to compete, and simplify the process of delivering accurate, repeatable colour quality from the press to press, job to job, and even plant to plant.
Are you in collaborations with the digital technologies in the web segment?
HD: We are in talks with digital companies like HP. The requirement from such segment is very different.
Will digital printing become a threat to the register control system?
HD: We thought it would be during this Drupa, but nothing has happened as of now.
Installations
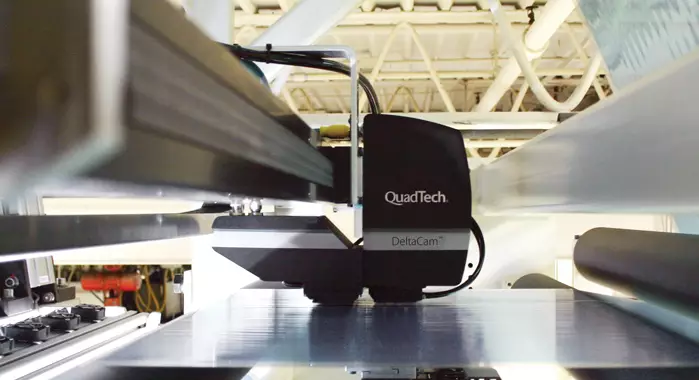
DeltaCam provides accurate inline spectral measurements, reducing waste
Register Control System 478 system for newspapers plus 10 for book industries, total 488 systems on around 1,800 towers/webs.
Register Control System 500 systems in flexible packaging segment.
100% inspection system 24 systems in flexible packaging industry.
Out of 10 newspapers you will find in stalls, 8-9 must have passed through QuadTech cameras/ controlled through our systems.
24/7 technical support around the globe. Night shift of USA is supported by Indian technical team thereby maintaining the 24/7 technical support.