Getting the Braille in just the right dot size
When the demand for Braille on folding cartons increased at Printmann Offset, it metamorphed from manual production to automation. This ensured it’s Navi Mumbai plant was up to speed in adhering to the code of practice for the standardised fabrication of Braille on folding cartons. In the Bobst AccuBraille, the company found a solution. Noel D’Cunha finds out.
05 Sep 2016 | By Noel D'Cunha
“Braille embossing through a rotary process on cartons with Bobst AccuBraille has overcome the bottleneck in converting,” says Tejas Tanna, a director at Printmann Offset (POPL), Mumbai.
Printmann specialises in pharma packaging. Tanna says, “When the customers started demanding Braille embossed cartons, we produced them using flatbed die-cutting and clamp-shell machines. This was manageable when SKUs were few. But with increasing SKUs, it became cumbersome to produce them on die-cutters, and long make-ready times became a serious concern. That’s when Tanna decided to invest in the AccuBraille.
Marching on
POPL is a part of the Printmann Group. Printmann was established in 1987. Starting with commercial print, the company diversified into packaging, initially carton packaging and then into labels.
In 1994, Printmann took over POPL then Veekay Graphics in Thane, converting the 18,000 sq/ft facility into a full-fledged packaging unit. Over a period of time, it has grown to become one of the leading print packaging companies specialising in pharma packaging. It also moved from Thane to its current location, a 50,000 sq/ft site in Navi Mumbai.
Among the substantial investment, the company made in its carton division, there were three from Bobst – two Bobst Novacut 106 die-cutting machines and an Expertfold with AccuBraille.
Tanna says, with increasing SKUs makeready times became a serious concern. Add to this the cost of tooling due to multiple ups too became a major issue.
But Braille is about raised dots that allows the visually challenged to read independently. “Consistency of dot heights and avoiding mix-ups were major quality parameters set by our buyers and this could be overcome using automation,” says Tanna.
Bobst AccuBraille mounted on the Expertfold was the kit Tanna opted for. It allowed the company to produce cartons that overcame all the impediments.
Customers comes first
One of Printmann’s clients is Cipla, a leading pharma company in India. The company manufactures an extensive range of pharma products besides others in personal care.
Cipla had pointed out the regulations in marketsacross Europe and that it is mandatory to supply Braille embossed cartons with highest quality and consistency.
The introduction of Bobst AccuBraille, Tanna says, has helped Printmann to achieve the parameters Cipla required.
Cipla has observed a remarkable improvement in quality as well as consistency of dot heights in the cartons supply by Printmann who are using AccuBraille rotary embossingprocess.
Reduced time-to-market
Today print converting is not just printing and converting the paperboard, it is also about ensuring just-in-time delivery which is obviously very critical to the pharma business.
“The changeover time and and setting on Bobst AccuBraille from one job to another takes under 15 minutes. Besides, we require investment on just one male tool strip to produce the job,” says Tanna.
Bobst presently has 28 Expertfold folder-gluer machine with AccuBraille modules in India. Two more are expected to be installed in 2016.
Braille Embossing – However You Want It
Braille, which is read with the fingertips, has cells. Each cell comprises of a rectangle with up to six or eight raised dots. The rectangle is no bigger than a fingertip. Can you explain how is the Braille produced using AccuBraille? And what is the tooling process with AccuBraille?
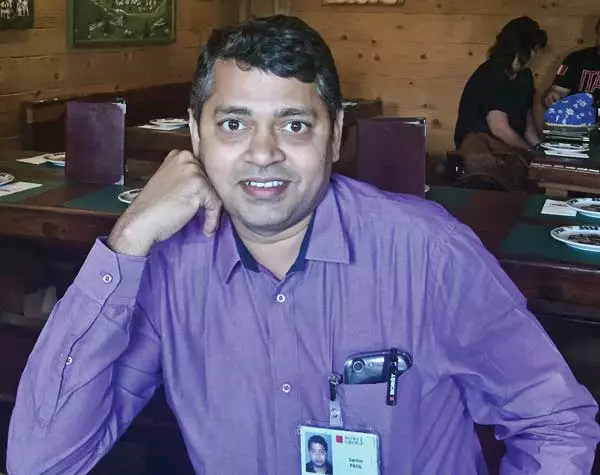
Braille characters are formed on carton through the embossing process. In AccuBraille, the embossing is done using a rotary process. This means, pressure is applied by a rotary tool as a line pressure. This gives better control and consistency on the embossing height. The formation of the Braille is standardised (2x3 dots). The female tools are common for all jobs, but the male tools are prepared as per the job requirements. The male tools is precisely made on specialised machine so that the dot height and diameter is maintained as per the standards laid down by the ECMA (European Carton Manufacturers Association).
Where does one get these tools?
These are available with Bobst India, as per the customer’s requirement.
Before large-scale punching, it is necessary to ensure that the dots are within the approved height. What quality controls are required?Can you also explain the mechanism?
The important point in Braille embossing is the position of the Braille dot and dot height. In AccuBraille, the side registration is done using blank aligner section positioned just before an AccuBraille module. The registration in the running direction is controlled by an electronic/software system. The pressure to get the desired dot height is maintained by a pneumatic system.
Is there a software that drives AccuBraille?
Yes, a software designed by Bobst controls and maintains the position of the dots. When the job is run on the folder-gluer, the gap between two cartons always varies. The Bobst software reads the edge of every carton arriving and then gives command to the rotary Braille unit to position itself.
Yes, the dots height is specified by the end user. The customer producing the Braille embossed carton has to do the quality assurance to check if the dot height is within the permissible limit. Normally most customers use a dial gauge to check the dot height.
Can AccuBraille be retrofitted to an existing folder-gluer?
The AccuBraille module can be retrofitted, but only on the Expertfold range of Bobst folder-gluers.
A word about maintenance of the kit?
We recommend regular cleaning of the Braille unit and the female tool.
(Sachin Patil, national product support manager at Bobst India)
Printmann Offset: The pharma specialist
Printmann Group has a patron in the 60-year old Bipin Tanna, father of Tejas and Ankit Tanna. Tejas is a print technologist while Ankit is a business and finance management specialist.

Printmann is PS 9000 certified. This means it has been audited and approved to supply secondary packaging materials into the regulatory pharmaceutical markets.
The Group companies, Printmann and POPL also boast of BRC/IoP certification.
The Group has three plants, including their latest foray in gravure printing to print on aluminium foils for pharmaceuticals.
Printmann is equipped with two Komori 20x28-inch perfectors, five Mitsubishi presses – three 28x40-inch size and two 20x29-inch size – plus two full-size Mitsubishi perfectors, and a Rotatek Brava. Besides the Bobst equipment, post-press include : two G&K Vijuk’s GUK FA53 outsert lines, another one GUK, installed in 2008, and two Herzog + Heymann machines.