Just-in-time throws up a challenge to operations folks to manage production under tight deadlines, and we need to plan meticulously, from raw material to deliveries, explains Tarun Sachdeva, operations head at Wolters Kluwer India, to Subhasis Ganguli
It has become a trend in publishing for production managers to take up additional responsibilities in operations. You were one of the first product persons to take up operations responsibility. What are the basic differences in your roles as a production manager and as operations head?
Compared to production, operations is a much larger role. When we say production in publishing sphere, it is usually restricted to manufacturing responsibilities. In few more evolved organisations, it also includes pre-press responsibilities of typesetting, copyediting, proofreading, designing and nowadays, it may include ebook conversion.
As an operations head, it is just one small portion of overall gamut of my responsibilities. I am currently handling complete supply chain management comprising of functions of warehousing, logistics, order fulfillment, customer relationship management, IT procurement, real estate procurement and facilities management in addition to manufacturing and pre-press domains.
For an organisation like Wolters Kluwer, which is more information systems company than a publishing company, content matters, delivery platform doesn’t. Hence my role involves co-ordination of content delivery through online portals, and DVDs as well.
As you are also responsible for stock now, does that effect your print decisions?
Yes. Inventory management is an integral part of my job now. I am responsible for inventory carrying costs and indeed it affects my print decisions now. Earlier, as production manager, I was only responsible for manufacturing and book developmental (pre-press) costs, but now I need to consider its shelf life, inventory carrying costs and provision for returns. Hence, I am much more vigilant when it comes to print runs.
As operations head, you are now responsible for the whole value chain. What are you doing to improve efficacy to the system?
The whole market is changing towards just-in-time inventory. Neither the publisher, nor the distributor wants to keep huge inventories, which throws up a challenge to the operations personnel to manage production under very tight deadlines.
To manage the same, we need to plan meticulously, from raw material to deliveries. While we want premium service from vendors in terms of scheduling, we can’t afford to pay more. So, the job allocation process becomes trickier, but with applied business intelligence, the challenges can be overcome. We have also started doing front-end XML instead of back-end for our locally developed products.
Where do you place Indian printers vis-à-vis printers in China, Hong Kong, Malaysia and Singapore?
I see most of our international and North American books being produced in China. In my opinion, it’s just not the printers, but the whole ecosystem that matters. From the availability of raw materials, to the overall infrastructure, warehousing and shipping facilities, China scores better. Our journals for global consumption are being produced at Singapore, as it demands a lot more customisation through variable data printing and mailing efficiencies. But recently, we did a costing study and in smaller print-runs, it was economical to print in India than anywhere in Asia.
Vietnam is presenting itself as a print destination in the international market. What is your experience?
Vietnam is coming up as a manufacturing hub. It is not only focusing on being a print destination, but also producing large volumes of apparels and electronics. Its liberal economic policies, stable political scenario and geographical position enhance its appeal. It is also churning out comparable quality and is offering competitive pricing. It’s a low-cost, high-volume market. My experience is limited, for our kind of runs, printing locally is more suitable.
In your opinion, what do Indian printers lack on their way to becoming a preferred print destination for international publishers? Which are the areas they need to improve?
A couple of Indian large-scale printers used to print for our US office a decade ago, but slowly and gradually, things have gone in favour of China. Like I said earlier, it’s not only print quality but the whole value chain that counts. Definitely, in terms of the scale of printers, infrastructural facilities and ease of doing business, India has to show much more agility. Printers also need to ramp up and become more efficient, enabling them to turn around large volumes at much faster pace.
About Tarun Sachdeva
Tarun Sachdeva says his professional super power is building a motivated team, multi-tasking and working across functions in a matrix to achieve the desired results. He is a graduate from Delhi University and an engineer in printing technology. He started his career as a manager at Pearson Education before moving to Wolters Kluwer, where he started as production manager but was entrusted with additional responsibilities of warehousing, distribution, facilities and IT. Currently, he manages the entire operations for health and TAA businesses at Wolters Kluwer.
His focus area is building result-driven, goal-centric and customer-focused centre of excellence within operations and supply chain function. He is also passionate about cars, reading about them and driving.
With your new position, how could you help Indian printers go global? What is your expectation from them?
When the printers are ready to compete in pricing quality and turnaround times, I can introduce them to right decision-makers and promote them internally. In my organisation, we talk of large volumes, and long-term contracts at highly competitive prices.
What is your take on GST? The general feel is that cost is going up…
GST is now more evolved. We had a lot of ambiguity earlier, until later notifications clarified the rate and applicability of the GST on manufacturing and royalty. It is an additional cost burden for us as the end product is exempt from GST, it being educational in nature. The basic objective of keeping books as an exempt commodity was to have lower cost of education but the purpose somehow got diluted with tax being levied on printing of books and reverse charge mechanism on royalty.
What has been your experience post-GST?
No printer has clearly specified what their input credit is. They are telling the GST they are paying on various components but they need to pass the input credit to the customer. We can say that the system is not that transparent and a bit complicated for now. But I also feel eventually competition will take the front seat and only a minimal cost burden will be passed on to publishers and readers.
All change is painful. How are you planning to cope with the challenge?
We are pretty well-equipped in handling changes. I had made my billing software ready and tested much before GST was implemented. Our finance team has a taxation specialist, who ran the GST implementation as a project and kept things ready proactively. They also involved third party consultants to guide all stakeholders like me through the process. There was some confusion initially on GST applicability on manufacturing but now things are sorted and well-adopted.
As head of operations, you are now responsible for stock holding as well as cash flow. So, you need to print the stock just-in-time and keep a control on print quantity to reduce wastage and pulping. What is your plan to mitigate these challenges?
Well, it’s a three-pronged strategy – plan, plan and plan. First, we need to plan the inventory meticulously; second, always be ready with plan A and B to ensure time availability; and third, plan print-runs objectively on the basis of past year trends, market landscape and growth expectations.
Do you think digital printing could help you overcome these challenges?
In few cases, yes. But as large portions of our product portfolio is multicolour and the costs are prohibitive in digital, I have not been able to adopt the technology to a large extent. Though I must say the quality has improved in the last few years. Now some of the machines produce almost offset-like depths.
There is no colour inkjet print engine in India. Do you think there is enough market for the same? Is it the right time to invest in that technology?
I think yes, although it may not suit the requirements of medical publishers like us. But for trade books, and school books, I feel the market is ripe enough.
Do you feel the need of a common forum, where you could meet periodically, share your knowledge and discuss challenges in a less formal environment?
Indeed it will be a great initiative. There are many common problems publishing companies and operations personnel go through. We will be able to share best practices, gather support and viewpoints on challenges faced.
Will you be ready to attend this forum organised by a third party? What is your take on such forum?
Yes, we will be willing to attend such a forum. It will be good to have a good representation of all facets and regions of manufacturing in the forum. We can have printers working for different niches, from different regions. If the forum is successful domestically, we can even take it international.
Have you considered PUR binding? If so, what is your experience with PUR?
I first heard of the term PUR in 2002-03, when I was coordinating the production of a dictionary for our UK office. The product was to go back to Europe and was required to be bound either by PUR or section-sewn. We did the order with section sewing but I have been following the technology since then. It is quite encouraging to see the way the technology has advanced in the last five years. I see a lot more adaptability to the technology now.
Do you think PUR could be a way forward to reduce turnaround time and to improve quality?
Yes, definitely. I see more and more printers and publishers adopting the technology going forward. There was a mismatch between technology and the weather of our country earlier. Now the technology has advanced and it can sustain extreme weathers prevalent here. It will remove the bottleneck of sewing; yet will provide a nice layflat product with a perfectly square spine.
Today, no publishing house has a laboratory of its own to test the end product. With the change in market and as awareness and expectation of the end customer is growing, isn’t it important to have a lab to test the quality before the stock hit the market?
It’s a nice idea. But with publishing houses focusing more on content than the medium, their focus is divided between print and digital forms. The print format is not growing as it used to. So, finding funds and additional space internally may be a challenge for manufacturing folks. But it is something which will empower them with more objectivity while allocating jobs, it will make the vendor selection process more scientific.
It is like preventive maintenance rather than reactive maintenance of the machines. As a market leader, could you take a chance on your reputation?
Publishers can’t take chances with their reputation and that’s why they try working with larger printers with better machinery and better substrates. It will be good to have a laboratory in-house where some basic tests on substrate and production quality can be performed, recorded, shared and used as a future reference for further allocation of jobs.
Though the onus is on the printer to deliver the right quality, it is important to specify your requirements correctly. As you may be aware, grain direction, gsm, bulk of a paper are important. It does not cost much to set up a small lab in-house. What is your take on this?
It’s an idea definitely worth exploring. It will be good to specify the pull strength on purchase orders in addition to the other parameters.
About Wolters Kluwer
Wolters Kluwer is a global company that provides information, and services. Its customers are legal, business, tax and accounting, finance and audit, risk, compliance, and healthcare professionals.
The company portfolio offers software tools coupled with content and services that customers need to make decisions with confidence. Wolters Kluwer excels at combining its superior information with the latest innovative technologies for use in the professional context its customers operate in. Its intelligent solutions incorporate open architecture networks in which it plays a hub role, coordinating activities and enabling communication across a customer’s workflow. The company ensures that its customers have the solutions they need, when they need them, and in the media best suited to their requirements.
Wolters Kluwer has 19,000 employees in over 40 countries, serving customers everywhere. The company is headquartered in the Netherlands and stock-listed at the Euronext Amsterdam.
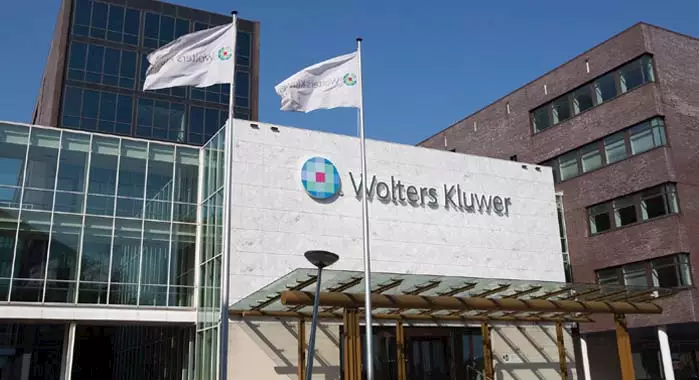
Wolters Kluwer HQ in Netherland