Digital doesn’t necessarily pose a threat to printed newspapers, but it must evolve with time. It’s time a newspaper looked like a prestige item, like an iPhone or a Cross pen.
For this, it must have three things — best quality paper, best content and best appearance, explains Snehasis Roy, one of the founder members of World Printers Forum, Wan-Ifra, in an interview with Rahul Kumar
The recent print media outlook by myriad agencies is positive. What’s the outlook at your print centres?
SC Roy (SCR): There are two aspects to this. First, English newspapers did not grow but remained flat. Revenue-wise, it was actually slightly negative. From the last financial year till today, the numbers fell by one or two per cent. The growth story took place in the language newspapers. All regional language newspapers grew at an average of 5%. Some even grew by 20%. Now, this growth refers only to circulation. In most cases, pagination numbers and total consumption of newsprint have remained the same. It is a balancing act. You grow by number, but your paper becomes thinner. I will not say that the situation is totally negative. Few publishers are even initiating new press projects. The number of new editions and new print centres are still growing for language publishers.
Your most challenging deadline in the last 12 months?
SCR: In newspaper production, you a have daily deadline and you have to meet it. You have to finish printing by 4 am, whatever the situation may be. We have started printing on glossy papers on our existing machines. UV printing on newspapers is becoming quite common. Earlier, we used to do four to five glossy covers in a month, but the demand is increasing in this area every month. Thus, you can see growth. That’s why publishers are putting more UV curing systems across the country. Challenge is to complete most of these initiatives before the festival season.
What technology methods (indigenous mailrooms; inspection systems) that have transformed your production operations in the past 12 months?
SCR: Again, the focus is in two sectors. First, the sector with high throughput and usage, where we do not want to compromise with indigenous development. Newspaper production is a time-critical operation and being a large media house, our production volume is very high. We have always opted for the best technology available. That may be Swiss, German, and American and may be Indian, but the best. There is no compromise with quality in that area. There are other systems like fragrance applicator, gluing system and others, which we do not use every day. We may opt for indigenous systems for such equipment and operations. Indigenous technologies are preferred for low frequency usages. Reliability is the factor in technology choice. We want the best of technology. It doesn’t matter from where it originates.
There have been many experiments with size in the recent times. Which print format, according to you, is best for India?
SCR: According to me, broadsheet is the best suitable size for the Indian market. We tried for tabloid but opted for broadsheet later. Indian market is not yet mature for a tabloid format. Indians do not take tabloid seriously. We experimented tabloid with education institutions but did not succeed. European and American markets have different stories here. It may be human psyche or we are used to broadsheet newspapers. Some financial papers were launched as Berliner and later got converted to broadsheet. Around three newspapers in the UK went from broadsheet to tabloid and again back to broadsheet. People find broadsheets more trustworthy. Newspapers have to evolve themselves. Future may be for the smaller size because of economy and ease of handling. Look at the pizza, when it came to India, very few considered it for dinner. People used to have it as snacks. But now, it is very common to have pizza dinner. Introduction of any new format takes time. Its acceptance depends on the maturity of the society. I believe, 533mm cut-off size is the future, if not less. We are using 546mm right now. ABP and Bhaskar are using 533mm.
What can the country do to better recycle print newspapers?
SCR: Honestly, recycling of printed newspapers is most optimally done in India. In other countries, people recycle newspaper to make new paper. In India, recycling happens in packaging. In India, we have multiple usages of printed newspapers — we put it in our racks; we use it for packaging of small items especially at local grocery shops. We are quite innovative in use and reuse of printed newspapers. Now even the press waste go down to landfill. First, we reuse printed newspapers and then we go for recycling.
Talking about waste management. What’s your waste ratio?
SCR: Most of us have two types of operations – one is our own printing presses and the other is outside printing operations (OSP). Wastage in OSP is higher because paper handling is done by the third party. There are some constraints. The transportation system is also not good to provide them clean and undamaged paper. Their wastage is higher than 2%, maybe 3% or more. Our in-house paper wastage is 2.4%, somewhere it is even 3%. Our wastage is slightly more. We are taking initiatives to reduce it and I can say that in the next one year we will be one of the low wastage newspaper production operations. We are running programmes and studies on reel stands performance enhancement. Better monitoring and maintenance of reel stands help a lot. Segregation of paper for night and day operations can also be very helpful. Also, it’s a good idea not to mix multiple gsm in one go. On a single night, use of the same gsm on a printing press will give better results. We are planning more automation for newsprint handling. Right now, around three to four programmes are going on. We are using 70% low gsm papers.
42.5gsm and 40gsm are becoming standards among Indian newspapers. Your view?
SCR: I agree. Maybe someday Indian newspapers will go for 38gsm. Of course, mileage is a major factor, but we shall try this without compromising on look and feel of the product.
We have a product in 40gsm which gives you the feel of 45gsm with an extra amount of PCC and advanced technology. New developments in newsprint technology and price pressure will drive the use of lower gsm paper in near future. If a newspaper production house reduces 2gsm in newsprint, then it may end up saving around 3% to 4% of total production cost. The number of pages per ton will be more and wastage will come down. Whenever you will go for lower grammage, it is a learning curve for the shop floor, which could be from a few months to a year. Then a newspaper house can see the benefits of perpetual savings.
Your top three print innovations in the past 12 months?
SCR: One is the personalised newspaper. Some people prefer to have their wedding invitation in the newspaper. Personal newspapers can be done on your birthday, marriage anniversary and other occasions, where the invitation is printed on the front page the customised newspapers. Second is HCP high quality newsprint printed in the coldset press. We are working on a project where we are using better substrate for better quality. We are also streamlining our way too many fold and flap innovations. We are trying and adding values from readers’ perspective.
What’s been the INCC audit journey like? What sort of dot gain variations do you see?
SCR: Dot gain variation depends on your maintenance and understanding of the process. If you have a good system where you can maintain your blanket height, squeeze pressure on the paper and others, you can achieve it. Press control is the key. You will not face problem for dot gain and it will be 3% to 4% spread across CMYK. However, INCC membership becomes tougher over the years. Printers who participated in INCC are surely capable of completing the process. We are using only FM screening for newspaper production.
What sort of centralised pre-press approach do you follow?
SCR: Our pre-press is not centralised but you can call it regionalised. Centralisation is not easy for us because we have many regional centres. If you see all of our titles from different centres, you will find that the entire newspaper is different except the masthead. For a newspaper house like us, regionalisation is better than centralisation.
How have you harmonised the process between all your print locations?
SCR: Being an industrialised newspaper, you have harmonised your operations. There will be the similarity if you will compare the Mumbai copy to Coimbatore copy, especially in quality. You have to follow some norms and standards, such as density control and profiling. All the pages must go through colour management software. Colour has to be maintained across the country no matter which press you are printing on. These are some of the ways you can harmonise your production.
Even today, the newspaper ad sales desk faces font issues, RGBs, low-re pictures, uncorrected pictures, PDF version issues, ICCs and so on from their customers. How do you counter this?
SCR: Most of these issues have been taken care of a long time ago. As we are a big newspaper house with prime advertisement space, more than a decade ago, we installed pre-flighting software. We have been normalising all our files. All of our advertisement files are pre-flighted, thus, any discrepancy can be highlighted by the system. It can be re-sent to the customer for correction if required.
What is a good average for web breaks per thousand reel? What is your target?
SCR: The Indian industry average is quite low. As per my knowledge, it is six to seven. Internationally, top newspaper houses have four to five. Our internal target is 2.5 to 3 and which we are meeting right now.
Some say the fake news is good for serious newspapers, as more people crave for solid journalism. Your view?
SCR: No, it is not. People read newspapers because of its trustworthiness. Credibility is the backbone for newspapers. Readers do not trust digital media as much as they trust newspapers. Readers consume digital media but they trust newspapers. There is no place for fake news in journalism, at least in the long term.
How can print media keep up with the ‘feverish’ pace of digital disruption in India?
SCR: I have been saying this on many forums: Digital is not disrupting print, it is disrupting media space. The print is fundamentally correct, long-term, and solid process. You have to understand the entire cycle of news. The print came to be the first mass media for news, then radio, then television came and then digital and new media. Not even a single medium of news has been stopped because of the later entrants. Readers are consuming from each source of information. Media never dies, it transforms and survives. Newspapers will also transform with new look and appearance. Newspaper houses have to understand the need of their readers, and this is the only way to survive and grow. The newspaper has to be customised, according to what a target group of readers wants to read. We see developments in terms of the good quality newspaper, especially in printing. The display is part of our life today. Readers need good quality newspapers.
Paid newspapers for future will be printed on better paper like books. People will carry newspapers like they carry iPhone and Cross pen. The future newspaper must have best quality paper, best design, best content and best appearance.
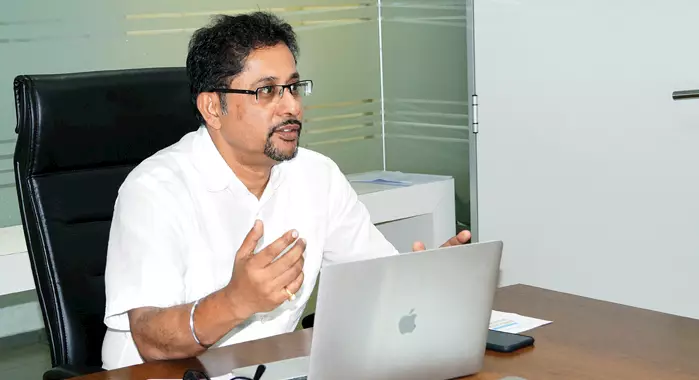
It has always been a challenging journey for me. I never had a tomorrow in my life
The print career of Snehasis Roy
Snehasis Roy, director technical, Times Group, started his journey into print as a student, when he joined the Regional Institute of Printing Technology (formerly, The School of Printing Technology), Jadavpur, Kolkata. He liked printing and he was the class topper. At the time, offset presses had just arrived and the industry was converting from gravure and letterpress to offset. He was fascinated by offset, and by colour reproduction. He completed his degree with a gold medal in 1982. This helped him secure a national scholarship and eventually, he landed at Rochester Institute of Technology (RIT), New York, USA.
Roy says he had an interesting time at RIT. He did some good projects with Miles Southworth and John Silver in colour and ink, and with Bob Chang in quality assurance. Those were his three gurus.
He got his first assignment to work on a cruise ship print house in Queen Elizabeth II. The size of the newspaper was A3. Total 5,000 copies of the paper were printed on a sheet-fed press every night. He worked alone, picking up news items from Associated Press, Reuters and other agencies, putting them on camera board and making a printing plate. It was a lifestyle newspaper, especially high-sea lifestyle.
He believes, in the newspaper, there is no tomorrow. Newspaper production at sea was the same.
Roy’s love for newspaper production, however, started in the early days of his printing education. After completing his studies at RIT, he got his first job in Time magazine. “I started working in Time magazine in its head office in New York. I got very good acknowledgement and also received prestigious awards,” he says. After three years, Roy returned to India and started in Jadavpur University. At 29, he was the youngest head of the department of printing engineering at the university. “I helped develop syllabi of three universities – Jadavpur at Kolkata, Anna University in Chennai and Jawaharlal Nehru Technical University at Hyderabad. The same syllabi are still taught at the universities,” he says.
The next stop was the Times Group. “I was the head of training, development and quality assurance,” he says. Later, he became the general manager of the Delhi (Sahibabad) plant. Then he moved to Bengaluru for a project, which included the installation of India’s first Manroland Regioman web offset press and Krause Violet CTP.
When the group purchased the Vijaya Karnataka newspaper, he was part of a five-member team to make the paper successful. During his first stint, Roy spent 13 years with Times Group. Then he moved to Dainik Bhaskar Group in 2007 as group head-technical.
Later, he joined ABP and installed the first Wifag web offset press in India. Roy considers it as one of his most successful projects. He spent eight years at ABP from 2008 to 2016. In 2016, he returned to Times Group as technical director.
“It has always been a demanding and challenging journey for me. I never had a tomorrow in my life. From the days of Queen Elizabeth II, I was hooked up in the environment of high-pressure delivery and loved it all my life,” he says.