Panthala Selvan of Pressman Solutions feels that colour management has seen a rise in the Indian printing industry over the past few years and more and more print firms are choosing to try it on their own shopfloor.
In an interview with Sriraam Selvam, he provides a microscopic view on how to go about predicting the colour of print and narrates his expedition into the world of colour management
Sriraam Selvam (SS): Can you share the brief history of your organisation? When was it established plus the team size and key clients at Pressman Solutions…
Panthala Selvan (PS): Pressman Solutions was established in 2009 at Chennai. Currently, we have seven team members who work from Chennai and Mumbai. Our clients are based in India, Sri Lanka, Bangladesh, Middle East and Pakistan. Few Indian clients from Western region are Navneet, TCPL, Temple Packaging, Parksons Packaging, Parksons Graphics, Ajanta Print Arts, Kalapi, Manohar Packaging and SAPCO (Shree Arun Packaging Company).
SS: How was your journey from being a print engineer to setting up Pressman Solutions? Do you recall your first client - and first case study?
PS: Pressman Solutions had begun with a different set of ideas and plans. One of our clients had inquired for calibration of a press. To cater to his needs I had enrolled at the Print Media Academy (PMA) to equip myself with some basic knowledge of pre-press and press standardisation. The project didn’t materialise as the client never confirmed. But from then on we included press calibration as a part of our profile. Later Thiruvananthapuram-based Akshara Offset was willing to opt for press calibration. I stayed on the shopfloor and it took me a whole week to complete
the project.
SS: How were the results? Did it lead to any new clients?
PS: The results were good. Whatever knowledge I had gained from Kodak; since I used to work for Kodak, and PMA got applied as a part of this project. It motivated me to focus more on press calibrations. Then a few newspaper houses from Kerala like Mangalam and Madhyamam approached us for press calibration and we never looked back. This process was accidental to us but today it is our only business.
SS: How did you gain the expertise apart from working at Kodak and PMA?
PS: I was also certified by Ugra as a Certified Expert in 2009. I had applied for it soon after the PMA programmes. The main idea is to offer professional calibration services with thorough knowledge that was gained through PMA and at an advance level from Ugra. Currently I am doing FTA’s (Flexo Technical Association) course for First Implementation Specialist and have cleared level one. This will enable me to cater to calibration services for flexo industry. G7 (grayscale plus seven colours) expert and re-certification for Ugra is on the cards.
SS: What are the various process standardisations offered by Pressman?
PS: We offer process standardisations for the complete print factory. We cover documentations, workflow designing, operator knowledge building, conducting workshops to demonstrate how to handle tools or equipment, annual training contracts and site preparation for Graphic Measures International (GMI) audits.
SS: What is the ideal implementation process for an Indian firm?
PS: Ideal implementation process begins with training the operators to break the mindset, teach them new things, introduce documents, setting targets and; measuring, recording, monitoring and controlling the process. Team building is important in this process. I feel this is the foundation for standardisation. The complicated aspect is to break the mindset and teach printing technology to operators who have more than 20 years of experience in printing.
SS: In the commercial CMYK print environment, a printer opts for ISO conformance (PSO) or G7 (grayscale plus seven colours) protocols for print process control? What is your preference?
PS: Whether it is ISO or G7 methodology there ought to be some kind of a standard for the printer to follow. Personally, we prefer ISO – 12647-2 standard. Usually, printers have no choice. We have done many calibrations to G7 as well (as a print buyer requirement). I haven’t compared the results of ISO against G7.
SS: Surprisingly, there are no statistics detailing the growth rate of software and hardware colour management solutions’ market. What are your estimates?
PS: I don’t have the right estimates of software or hardware installations. Although I can assure you that the installation rate is growing at a steady pace. Many middle and top mid segment printers started investing in colour management systems. One of the main reason is that the buyers have started rejecting the print jobs for colour variations. Another reason is that the printer wants to offer superior quality than the competitor. This trend is only visible in the packaging segment. Very few commercial printers are considering these investments.
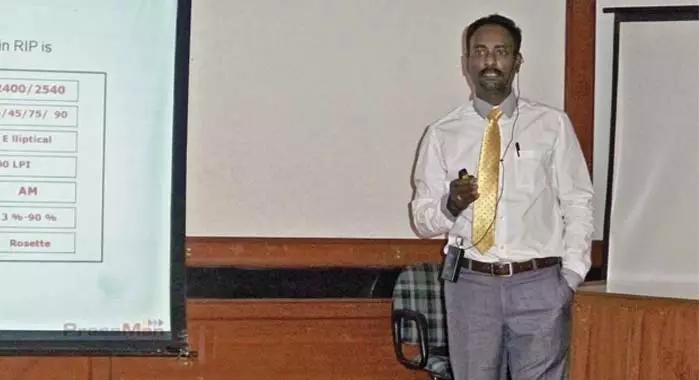
Panthala Selvan conducting a workshop
SS: The mystique of colour management still prevails in the majority of our industry. Spectrophotometers and software are a sight that is still restricted to a few. What has been the major hindrance?
PS: Many. Fear of not using it effectively. Customer not demanding quality. Underestimating the skill level of the workers. Taking feedback from press mechanics and operators to decide about the investment in these tools. This feedback is most of the times about the need for a new machine or it is a complaint about the quality of raw material. Rarely or never about the need for such tools. Then there is this concern of the trained guy quitting the job.
SS: You have been conducting workshops across India. What is the feedback you hear from small and medium firms who are keen to set specifications in the production process? Please explain with examples.
PS: We have a printer in a small village printing wedding cards. In the nearby five districts, he is the only printer using CIP3. It is the most basic version and it simply cost him Rs 50,000. He has also invested in a colour measurement system that cost him an additional Rs 2,50,000. With this basic investment of Rs 3,00,000 he is running his jobs compliant to ISO 12647-2 standard. Although it’s a small print firm it is able to provide the desired print quality and tops the group in that region. It has turned out to be a wonderful case study. Because the length of the job runs varies between 500-2000 sheets which is a small amount. And it’s because of the print quality that this gets compensated by him doing more jobs in a day. A particular print job getting printed on two different presses on his shopfloor provide the same result. This is because the firm matches Delta-E value for CMYK and not density. The only language heard on the shopfloor is delta error, dot gains and grey balance. The firm undergoes through periodic press calibrations and training programmes and this has become the culture there. The most beautiful aspect of this case study is that the customers of the firm are not demanding the quality. The owner is simply doing it for his own satisfaction.
SS: What are the tangible steps you have undertaken to improve the same? (if you can help and elaborate with examples)
PS: We create awareness, educate printers through Whatsapp groups, blogs, FAQ sessions published in print magazines, onsite trainings and seminars. Such initiatives have been helpful to a lot of printers especially when they need any sort of clarification. We keep an ongoing interaction with the operators and the management and conduct regular visits to inspect the printed sheets or ask them to send the samples at our evaluation centre. We continue this drill with regular reminders and text alerts. When it comes to colour, we are always the first point of contact.
SS: Can you enlist three daily steps which a print firm can follow in order to monitor quality?
PS: The primary step is to record the date for everything. Measure the water conditions and record. Measure the colour and record. Inspect the machine and record.
SS: In the Indian scenario, print firms who prefer colour managed workflow are those who print for international print buyers or those who cater to premium jobs where colour accuracy is important. Do you think this is correct and if yes, how can this be changed?
PS: Absolutely. Printers invest in colour management workflow because international buyers demand this system. The real advantage is known to them only after they start using this system for other jobs. And eventually, this system starts getting applied to all the other jobs. This can only be changed if the print firms stop waiting for the buyer to demand this system. They can always take feedback from other printers who have successfully followed it. The system needs to be tested by the print firms before investing in it. The knowledge of the service provider plays a vital role in implementing such systems. Let me put it this way: Colour accuracy is a basic factor that needs to be maintained by all printing press owners. As simple as that.
SS: Can you shed some light on Pressman Academy for Print Education & Resource (PAPER)? Especially your work in lamination and UV?
PS: PAPER was established two years ago for the operators to get educated in standardisation. The focus on lamination and UV was created through blogs which were a result of a question posted on the Whatsapp group by one of our clients. We did the UV tests for him at the Siegwerk lab and the lamination test at a client site in Bengaluru and posted the content on the blog. Additionally, we took information from various experts, accumulated them and compiled the information in a way that can be read and understood by anybody.
SS: What are the major trends and best practices in terms of standardisation you have seen in the industry both globally and in India?
PS: Press calibration to an ISO 12647-2 standard or G7 (grayscale plus seven colours), implementing Standard Operating Procedure (SOP), following basic quality checks by measurements and internal training programmes. Global standards like Lean production (the principles of which are derived from the Japanese manufacturing industry), 5S (workplace organisation method), SAP (enterprise resource planning or ERP system) are some projects that many printers in India are considering to implement. Such standards come with an added advantage of enabling the owners to let the factory run in their absence.
SS: Which standards are a must-know in today’s India? ISO, PSO, 3DAPv3, TVI curves?
PS: Print firms can begin with ISO 12647-2 or G7. This is mandatory.
SS: How frequently must one print a test chart to capture colour characterisation to create profiles for use in pre-press?
PS: There is no specific time period for this. Printers can use ISO / Gracol (General Requirements for Applications in Commercial Offset Lithography) profiles and set their pre-press / print standard conforming to these profiles. No need to create custom profiles unless it is for special inks or substrates. So ideally every job should be an ISO certified print or conforming to ISO standard. Whenever the prints surpass the tolerance level it can set it back through the process of press calibration.
Case-study: achieving colour accuracy with the use of right substrate
This particular project took place at Dhaka in Bangladesh. The client had to print a test chart on a specific substrate (grey-back board) conforming to a particular print buyer standard. This standard was close to ISO 12647-2 standard.
There was scoring for the print result. The requirement was 90% of the standard. We needed to strike CMYK dE (Delta-E) value of less than five.
Then there were areas like board (substrate) dE, overprint, trapping, dot gains, grey balance all within the specified standard.
Customer expected grey-back board whiteness equivalent to white-back board. Since the board dE was completely out of tolerance level, we couldn’t hit the CMYK dE and other parameters. We tried with all available boards from the local market. Due to variation in board colour, we couldn’t hit CMYK dE within tolerance levels. We even tried different ink sets. Finally we found a particular board that was close to our requirement. Half of the board was very good (the score was 90%) and the other half was 80%. Now we had to use three brands of inks to hit CMYK dE on that board.
Finally we scored 90% as average and passed the test. This was stressful for us as well as the owner. Somehow we succeeded at that time.
One month after that when the printer’s client visited the shopfloor for an audit, we had to reprint and get the same score in front of them. But this time around we imported the board from India and the results were above the 90% score and that too within an hour of loading the job.
The basic lesson from this case study is that achieving colour accuracy is easy when you have the right substrate.