Use of high resolution and high definition in flexo - Part two
In part one of this two-series article on pre-press in flexography, R S Bakshi dives deep into the technology to find solutions to reproducing rich coloured labels and saving costs as well.
29 Oct 2014 | By R S Bakshi
This system is in practice even today with most printers and the printer is happy that he was somehow able to produce a result that his customer approves, not with-standing that this results in losses like low press speed; frequent cleaning of blocks, leading to stoppage of press and increased substrate plus ink wastage and press down time; increase in cost of printing blocks and DSA tape for printing of solids and tonal shades separately on separate print stations. This results in increased cost of makeready and register setting time. Several more points could be added but this is not the time and place to discuss this.
The purpose was to see the printed result with each and compare, everything else remaining the same. The printed result is copied and reproduced alongside(below and on the next page). In addition to this several segments of the printed sheet were copied and enlarged to show the difference in the printed results which is visible very clearly. The printed images shown are arranged in the same sequence (a) taken with conventional anilox roll (b)taken with GTT metering roll and (c) the image on plate. When you look at the enlarged pictures of the segments one can clearly see that:
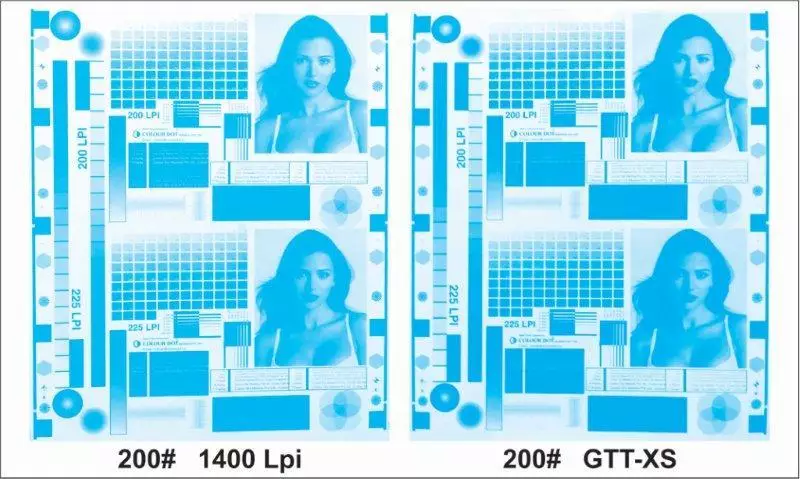
1 The thin lines printed with the GTT roll has a clean and smooth edge compared to the conventional anilox roll in each of the pictures.
2 The print shows that the plate prints more uniformly with the GTT metering rolls as compared to the conventional roll used.
8Since the GTT enables the flexo printer to print a higher density, the prepress will have to be modified to use this to advantage.