Ravi Kiran, director at Valco Melton India Engineering talks about the new Bengaluru factory, the company's Ero acquisition and how glue dispensers are becoming more and more automated
Valco Melton recently acquired Italy-based Ero. How is the acquisition the best fit?
Valco Melton is one of the oldest adhesive dispensing system manufacturers in the world. There are various industry segments that require different adhesive solutions and every application is unique. At Valco Melton, we have been developing the latest ways of glue dispensing and quality assurance systems and also acquiring various companies from similar industries who have innovative product range that can add value to Valco Melton’s portfolio. Italy-based Ero has got a wonderful product range for the folding carton industry with very economical pricing, so this acquisition will help us in the emerging markets like India. Valco Melton has got full flagged sales and service course in all the parts of India so it will be very easy for us to cater to the applications that demand Ero products.
Can you shed some light on Valco Melton's expansion in Bengaluru?
We have started our first manufacturing unit in Bengaluru in January 2017. This is also the first hotmelt dispenser manufacturing unit in India and also the first Valco Melton manufacturing facility in Asia. Valco Melton India has been selling the significant number of hotmelt machines and has a major share in global hotmelt glue dispenser sales. Therefore, the management found that it is the right decision to manufacture the systems locally to better support Indian customers.
What happens at the factory?
It is a 20,000 sq/ft facility three-storied building. We have 8,000 sq/ft of manufacturing space and 5,000 sq/ft space for the warehouse. The remaining space is used for the service centre, demo lab, and customer support centre. Here we manufacture the D4-e hotmelt system for local as well as the export market. We have a capacity to manufacture 500 systems in a year. We sell about 200 machines in India, while remaining machines are supplied to the global market. We also manufacture hoses at this facility.
What are the changes that you have seen in the adhesive dispensing field in the last two years?
The market is gradually adopting automation. There are several reasons for increase in volumes, need for quality gluing and expensive manpower. So the companies are investing in latest technology. Now, this has created a plethora of new opportunities which never existed before. Sometimes we learn new applications from our customers which we have never seen before. The market has become dynamic and is rapidly growing.
One of the most common problems in the use of adhesives is nozzle clogging. What are the factors?
The adhesive systems that are installed on the production shopfloors where the environment are conditions are dusty. Even a tiny particle of dust can clog a nozzle. In order to prevent the foreign particles from entering the system, Valco Melton machines are equipped with filters in systematically planned locations. Plus these machines have an option for self-cleaning of nozzles.
What are the costs that a blocked nozzle incurs to an operation?
The downtime is always expensive. There are costs at so many levels that we cannot calculate. At Valco Melton, we empathise and care about this. We have zero cavity applicators that can handle this challenge easily with self-cleaning nozzles and clean the nozzle blockage.
There’s a buzz about Industry 4.0. How does it relate to Valco Melton?
Our machines are capable of remote access. The user can monitor the quality of adhesive dispensing and can remotely eliminate most of the problems that a machine has by using the network. Valco Melton's camera inspection system, Pack Check can eliminate any unglued or bad glued boxes from the production line and can give you an assurance that there are no bad boxes in the line. These systems can generate various types of reports related to adhesive dispensing. This is in line with the ideology of Industry 4.0.
When it comes to adhesive, how important is the maintenance of adhesive dispensing systems?
Maintenance is critical. This is true especially when we speak about hotmelt systems because the hotmelt adhesive is melted at high temperature like 160-170 degree Celsius and then dispensed. Therefore, good ambience and regular maintenance can prevent sudden breakdowns. Our technology such as zero cavity modules or all electric systems has got very few moving parts, which reduces friction and avoids frequent maintenance.
Corrugated boxes: Stitching versus gluing
Comments from Bob Taylor, general manager, Valco Melton India
Although largely unused in Europe and North America, the use of stitching has remained a common method for corrugated case making in India. The eventual change in market demands was started when the blue chip companies in food, beverage and consumer products chose India as an ideal manufacturing alternative to more developed locations, with its lower overheads, and labour costs as well as hard-working labour pool.
These companies were, however, looking to export their Indian production back to their major markets and with this came the need to have recyclable packaging. Stitching was therefore mostly not permitted as the packages containing metal staples and could not be deemed recyclable. So gluing became the requirement to satisfy both this aspect and the increasing demand for volume production with lower costs to match the container unit prices in the developed home markets.
In recent years, we have seen an explosion in the number of packaging companies with high-speed in-line gluing. Gluing the side seam using PVAc is considered to be fully compliant with recycling demands and provides strength beyond the original substrate.
When adhesive is applied usually in a bead form, the two parts of the case are brought together under compression. As the composition of the glue is roughly 50% solid and 50% water, the water migrates into both sides of the board as it is compressed and draws particles of the solid glue with it into the fibres of the board. This results in a bond which develops over the next few hours to be stronger and produces ‘fibre tear’ when tested - conforming to all requirements of the customer.
Staples are more expensive than glue
• Staples weaken the case as the flutes are crushed
• Staples are unattractive on premium boxes
• Potential for injury from sharp staples
• Higher level of maintenance on the stapling machinery
One of the customer case-study of cost comparison reveals that cost per case of glue versus stitching is similar but productivity differences are dramatic. While stitcher produces 2000 to 3000 boxes per hour, a folder-gluer throughputs in excess of 8,000 boxes per hour. The Indian converters sell 80% of their box production to FMCG and food producers where staples are now not permitted. Our customers expect 100% of standard boxes to be glued by 2020.
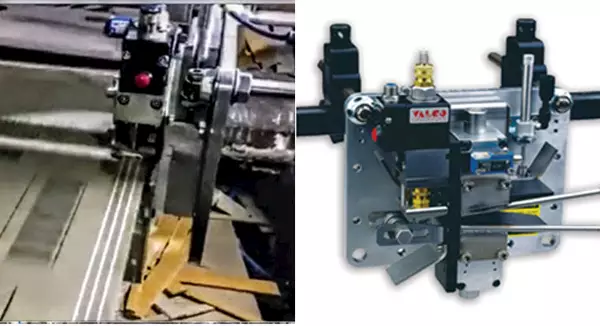