Brilliant Printers is hoping to up its capacity after moving to a new larger factory to boost its capabilities and service to customers. Publishing pundit Subhasis Ganguli is mighty impressed with the two years journey of the 1,53,000 sq/feet book factory.
Around two years ago, in 2014, when I visited the workshed of Brilliant Printers at Nelamangala, I was a bit concerned. My concern stemmed from the fact that the Rego family ( Anil, Sunil and Manil) were pouring their meagre assets to create their dream project. I studied the floor plan with Anil Rego and dark thoughts flashed through my brain (in no particular order).
- Why do other Indian printers not plan in the same systematic manner?
- Why do print buyers in the publishing industry not insist on a proper workflow?
- Oh, how beautiful it would be, if this factory could be located nearer to a sea port or near Delhi
- Could the Regos sustain such a huge investment and reap the benefits of a true-blue ROI?
- Has Brilliant identified the opportunity to save their monies through efficiency in order to justify the investment?
Above all, I was mighty concerned with the magnitude of investment and about their plan to change-the-game.
Two years later, I returned to Bengaluru and decided to visit their facility.
It was around 9 March, the day of the official inauguration function. The who’s who of Bengaluru were present at the 1,53,000 sq feet area facility at Mallarabanawadi, Nelamangala in Bengaluru which has “all processes executed under one roof, with consistency in quality, delivery and deployment of cutting edge technology”.
Brilliant boosts capacity following relocation
It was a nice long drive from the city to their new sprawling new facility. The shopfloor was humming with book-making activity. All the press machines (one eight-colour, two four-colour, one two-colour perfector and one single colour) were up and running. There was a buzz in the air.
In addition, I noticed the 40-inch Timson and three two-colour and one four-colour coldset web engines were all busy. As I stood at a height, near the allotted office space (yet to be built), I could survey the entire factory layout in-one-single-panaromic-vision which was identical to the plan that I had seen 24 months ago. Anil Rego informed me that they are planning to add one more Timson soon. This makes sense. The business has been growing and the Regos are putting quite a bit of emphasis on hardcore book manufacturing – so logically it made sense to look for “a bigger beast”.
Brilliant seeks re-invention
The thing is, every single organisation needs to reinvent themselves from time to time by restructuring, adopting new workflow, reviewing and implementation of best practices and more importantly make the organisation lean. In today's world, speed is the key and it is important for any organisation to reinvent the process to make the decision faster so that there is no gap between final delivery and commitment. The process and raw materials need to be standardised, demand planning and procurements must be robust and the best rate could be achieved through bigger scales. This system brush up is required to cut down the flubs which have accumulated with every year of passing. The flubs increase the costs, unnecessarily. As the organisation gets older and bigger, red tapism creeps in to slowdown the process. Plus there is a diffidence to change. This halts growth, and the organisation needs to pay more attention to tackle internal challenges if they need to survive.
It is amazing to see the meticulous attention that has gone towards designing the floor layout and the work done to make "the operations" a reality. It was a breathtaking sight to see a sprawling 153,000 sq/ft book factory with a complete linear horizontal workflow without any material lying around. The process, seamless and efficient. There is an exclusive 40,000 sq ft area allocated for paper storage in addition to the main plant.
50 Languages under one roof
I am informed the Brilliant story begins in a 100 sq/ft. rented office in the busy Chickpet area in the Central Business District in 1970 with a modest treadle machine. The firm gradually grew in production capacity and numbers, and shifted to Doddaballapura in 2004 and now to the new and much expansive location, where all the services could be under one roof. With this move they also have addressed the much required changes in workflow. From the early journey that began with a treadle machine, it is amazing that now the factory can export to more than 70 countries besides printing Bibles in more than 50 world languages. It is no easy task to handle many foreign languages at one go.
The Phase III
The new modus operandi enables Brilliant to work closely with their key partners, plus pick up some more accounts.
In real terms this means, a shift from its earlier factory location at Doddaballapur, Bengaluru to the now. This is phase III of a journey that began in 1970 with a treadle machine. All processes are linked through seamless integration of material and information flows along with synchronised product/process layout configuration.
As Anil Rego says, "All the post-press processes are under one roof, with a daily production capacity of 100,000 perfect bound books, 50,000 saddle stitched books and 20,000 hard cover books. Fully automatic binding and finishing machines for case making, book block making, casing-in, gilding, gathering/binding/trimming, shrink-wrapping, box tapping and strapping etc."
With the numbers Brilliant notches up on their daily production capacity quota, it is not an easy task to achieve optimum output, each and every day. Yet Brilliant is getting that with their old machines, which are in very good condition. They pay a lot of attention towards regular preventive maintenance and keep their machines in a good condition. With six sewing machine, three multi clamp perfect binding machine, two flow line and one hard case line with one automated case making machine, it is a complete and compact unit.
Tribute to Antony Victor Rego
With this one single move, Brilliant has addressed most of them, if not all.
Which is why, it has been a rewarding journey, thus far. The Regos credit the vision of the Late Antony Victor Rego( A V Rego) for planting the seed.
Anil Rego says, "A V Rego was a person with passion and dedication. He never compromised on values. An eye to quality was his hallmark. These virtues have taken the company to great heights and to the leadership position that it is in today. The culture of hard work at the press are his guiding principles for the entire workforce. Humility is another virtue that he always wore on his sleeve."
Printing the Holy Book
Not just that. As Anil Rego says, "Brilliant’s use of 28 GSM (gram per square/meter) opaque tissue paper (OTP) which is most suitable for printing voluminous texts in Bible printing model has been hailed. Bible printing operation is an art. Complexities include precise controlling of print margins, ink density and uniform spread across the page, printed matter opacity."
Brilliant is a master in printing on thin paper. They print on as thin as 28 gsm opaque tissue paper, which is most suitable for printing voluminous texts in Bible printing and dictionaries. It is a complex process to handle and print on such thin papers.
There are many challenges:
- Availability of the paper
- Opacity of the paper and see through of text
- Density of the ink
- Back to back registration
- Handling of paper
- Handling of printed formes through process of finishing
- Sewing of thin paper
- Binding
- Side edging and gilding
Controlling waste
Waste is a crime. It is no easy task to manage it. At any point the wastage could shoot up. This is usually due to a tiny unnoticed mistake in the process, be it ink flow or water control. At times, even alcohol damping, PH and conductivity of the machine could play role in creating problem while printing. Binding is another challenge. But, it seems Brilliant has mastered the art and the range of books they produce is pretty exhaustive. It is possible because of years and years of technical knowledge and grasping the ground reality by Anil Rego and his siblings, Sunil and Manil. They are focused about their requirements and crystal-clear about what they do not want to do. That could be the key of their success. In addition to their willingness to grit their teeth through the learning curve, they have a patience and healthy attitude towards change.
So, my question was how do they manage it? The answer is good old best practice followed by most of the book factories across the globe. Strict adherence to a job ticket and a policy of zero-deviation. Brilliant has reduced WIP time on floor. So, what they are printing is getting converted within the stipulated period to finished books and there is no stagnancy on the shopfloor with odd formes. Moreover, all real time job status is available with the customer service team. Any break up in the workflow or delay gets escalated to the daily production meeting and action is taken accordingly, says Naveen Rodrigues, the general manager. With all facilities under one roof, linear workflow and strict control of the process, helps them to control TAT and to fulfil their commitments towards their customers.
For finishing they have lamination, foiling, gilding and corner rounding machines under the same roof. They also have one PUR binding machine. This is not in use as their customers do not need that service. But, they will be ready to move fast if the demand arises.
Green theme at Brilliant
In addition, I was amazed to see the environmental awareness among all stake holders of Brilliant. Not only are they environmentally compliant with waste treatment, water treatment, electronic water control system in taps to control waste of water, the matriarch, Irene Rego gets involved in cleanliness and landscaping the areas outside the factory to make it greener.
All this needs a huge expertise in handling thin paper and to handle 50 different languages to serve 70 countries. Kudos to Brilliant team for this stupendous effort and to make it possible. I wish the Brilliant family of more than 400 people all the very best with their new book factory. One among the best in India.
The Brilliant factory
The new facility at Nelamangala boasts of dedicated diesel generators for power back-up, central air compressors, state of the art effluent and sewage treatment plants, rainwater harvesting technologies, dust-free/controlled atmosphere for sheet-fed printing, plate processing/exposing, sewing and case making sections, flow oriented layout for production processes with built-in lean manufacturing practices, neatly marked wide green walkways for safe human resource movement and wide gangways for seamless material movement, automated dock levellers for containers berthing, loading and unloading, earmarked areas for optimum storage of work in progress and finished goods inventories etc.
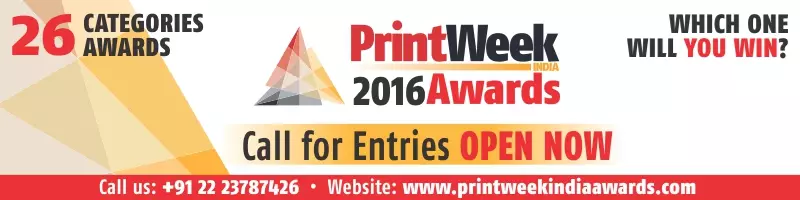 |
|