Welbound Technical Services: A brand independent service provider
Recently while visiting a press in Latur, the owner brooded about how his folding machine which he had invested via a second-hand dealer was lying idle on the shopfloor since a year. When asked why, he says the manufacturer is refusing to service it, as the folding kit is from a third party plus there was no other service provider who can do so. In another instance, a firm was struggling to complete a high volume export order of books due to the breakdown of its perfect binding line. Now due to
22 Nov 2017 | By Priya Raju
In addition, there are instances of sophisticated auxiliary equipment like PUR gluing systems that come along with pre-owned bookbinding machines, dry-laminators or folder gluers. Sourcing local support is most onerous for these. A bookbinder almost broke down when he was told that the control systems in his recently acquired, the pre-owned binding line is out-dated and cannot be supported. The only option: go for a conversion that will cost him more than his binder. In most cases, the user will be asked to invest in an enormous list of spare parts or send them to Europe for refurbishing.
Does this sound familiar?
In India, we rarely have dealers who have a facility for refurbishing machines. The “dirty job” is for the overseas companies, and our dealers get machines from them. The Indian dealers of these original global brands often help in checking the history of the machine, which is intended to be purchased. If a machine is purchased on “as is where basis is” then no service or guarantee is expected from the dealer. Some of them give guarantee for “satisfactory commissioning of the machine. PrintWeek India firmly believes that before the purchase of a machine, a thorough inspection is necessary, a trial too if the machine is still in production. All these will have the built-in stacking of commission, service charges and a package of spare parts.
For any aging machine, whether newly acquired as pre-owned or has gracefully aged in your own shopfloor the options for a printer or converter is to depend on either the support from the brand or the Indian representative or the last resort, a freelancer.
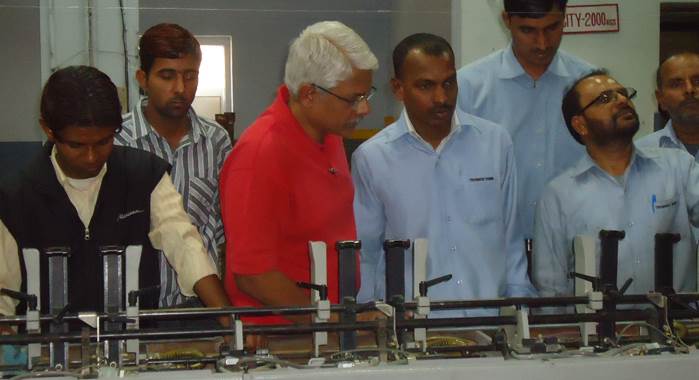
Training for the maintenance team in Thomson Press
Addressing the pain
Today, the brand Welbound is synonymous with service in the print and publishing industry alike. And for the past three decades, the manufacturer of book binding machine has been building a 60-member strong technical service engineer team to cater to its clients. Welbound Technical Services (WTS) was conceptualised to address the above pain points of printers and converters who seek “pure services” and unbiased advise on pre-owned equipment for post press.
WTS is the brainchild of P Sajith, director of Welbound. He says: “Print industry will undoubtedly tide over the onslaught of digital disruptions and the confusions created by GST. And by then we need to be super-efficient and extract maximum benefits out of our current investments. For this, investment in hi-tech equipment is not a solution. It has become increasingly important to understand one’s current capacities, strengths, weaknesses – and device a plan to enhance efficiencies.”
This is where the WTS team is geared up to play a supportive role. Sajith shares, “Our service engineers and application specialists have hands-on experience and in-depth knowledge of the process, substrates, adhesives, machines – design and maintenance, electronics – PLCs, drives. This is from their experience from servicing our perfect binding and other post-press machinery from our partners, which has been installed across India.”
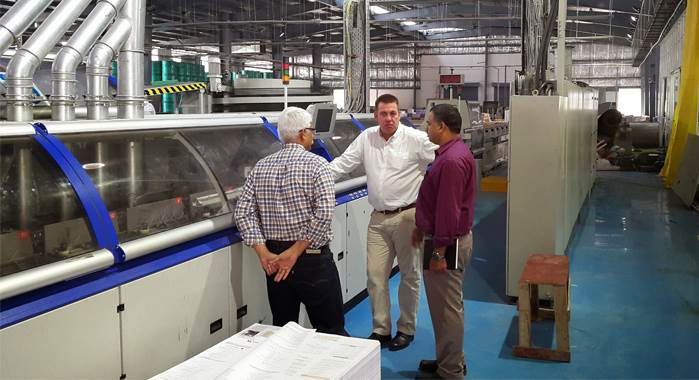
Post-installation audit of the Kolbus line
Brand independent support
WTS is in action. One such example for this was at Mumbai-based SAP, wherein Welbound sent its engineers to inspect the machine in Indonesia, helped dismantle, pack and unpack, and finally assemble, install and commission the machine at its premises. Other firms where Welbound had provided support include Manipal Technologies, S Chand & Co, Thomson Press, CDC Printers, Brilliant Printers, to name a few.
One fundamental feature of WTS’ offering is: to provide services to all types of machinery in the entire post-press operations irrespective of the brand or make of the machine. The applications and brands covered by WTS include all brands of machines for bookbinding, folding, gathering, binding, trimming (both soft and hardcover applications). In converting and packaging, support is offered for miniature folding machines – for insert and outserts of G&K Vijuk, guillotines of Wohlenberg family and any brands of folder gluers.
“We can also address any complex electrical issues of any machines. We have brought to life many machines that were written off due to the failure of out-dated motor drives Or PLCs – by replacing them latest drives and PLCs. We do the complete integration include software programming. This provides complete freedom to the customer”, says Arvind Kalasur, who leads this initiative. Kalasur comes with two decades of experience leading service activities of European manufacturers of post-press equipment.
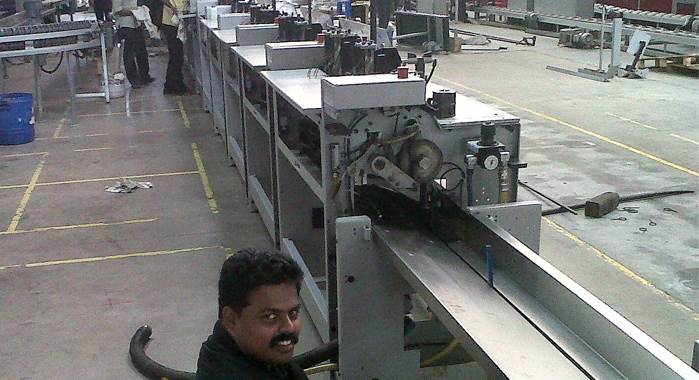
Acoro A5 installation at Manipal
Welbound effect
Talking about the WTS proposal, Sajith says, “Once the agreement is inked, WTS will ensure periodic visit of service engineer and application engineer, complete inspection of machine, immediate repairs required, planned service in near future, spare parts recommendations and our engineers will ensure the complete mechanical and electrical maintenance is looked after too.”
“Once a print firm entrusts us with its services and maintenance, they can be rest assured that their operations are hassle-free and efficient, and extract maximum benefits out of it,” says Sajith. According to him, the print firm can benefit from “additional support” which will include advice and support for machine settings, maintenance, improve efficiencies, operator training, new product trials etc.
Some of WTS’ reputed customers for services include Printmann, Pragati Offset, Hi-tech print services, for folding machines and Guillotines; Manipal Technologies, S Chand & Co, Brilliant Printers, Parksons Graphics, Replika, CDC Printers, etc for bookbinding machines among others.
“Outsource your maintenance worries to us - WTS will prove to be a perfect partner to you,” signs off, Sajith.
WTS services: at a glance
Services/ Audits offered |
Examples |
Machine condition assessment |
· Present machine efficiency
|
Chronic issues |
· Machine related problems that affect efficiency
|
Workflow analysis |
· Application-related issues
|
Machine productivity |
· Rated mechanical speed
|
Human resources audit |
· Present operator skills
|
Maintenance plan |
· Current maintenance plan
|
WTS offerings
WTS offerings include support for commissioning pre-owned post-press machines: inspection, installation, training, modification, annual maintenance contract (AMC); technology upgradation; modifications, configuration change and add-ons in a machinery, plus standardisation of electrical/electronic; audits and consultancy for efficiency enhancement: process, plant, machines audit to understand gaps and improve efficiency and finally, training services for operations, maintenance and application.