Picture Gallery: Taxi Fabric
Taxi Fabric made its modest beginning as a Tumblr blog in 2013 that simply collected the bizarre and quirky seat covers and ceilings of taxis in Bombay.
It is now a full-blown project that mainly collaborates with graphic designers to create exclusive theme based designs for the seat covers and ceilings of Bombay’s omnipresent black & yellow taxis. It has unleashed about 23 refurbished and inimitable taxis into the city so far. To delve deep into the Taxi Fabric story, we meet Sa
20 Jan 2016 | By Shripad Bhat
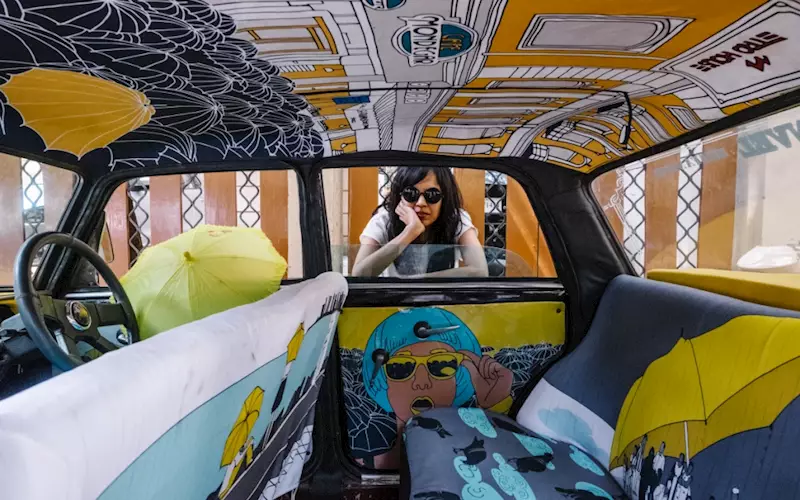
While earlier the Taxi Fabric team used to get in touch with a set of graphic designer friends, they now work with people who get in touch with them
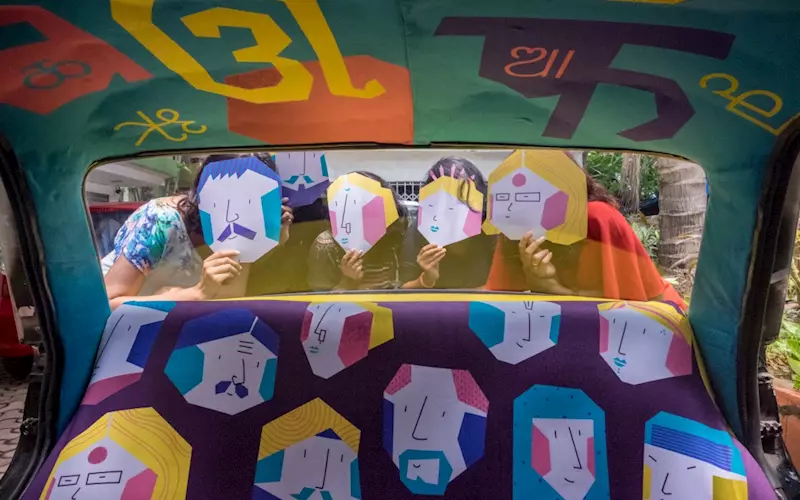
They don’t put a full stop to the selection with just the designer’s portfolio, though. It’s a huge responsibility when you are talking about 10 meters of fabric, and the designer has to show the ability to deal with that, Avlani specifies
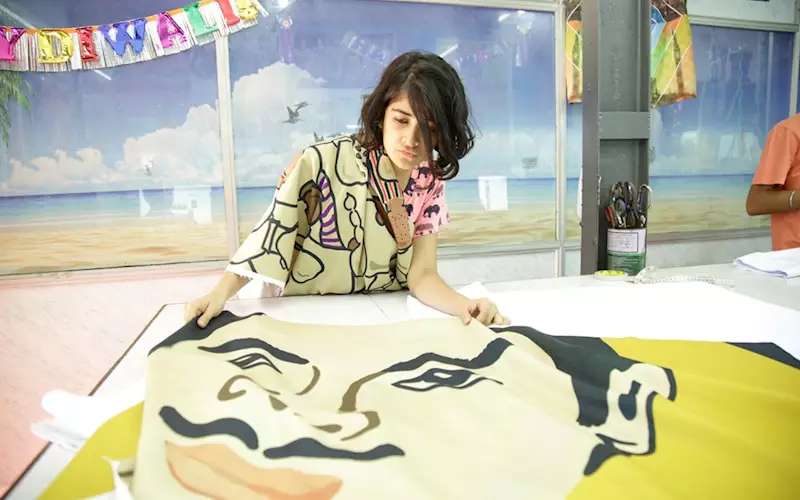
After the concept is finalised, the design process kicks off with some rough sketches
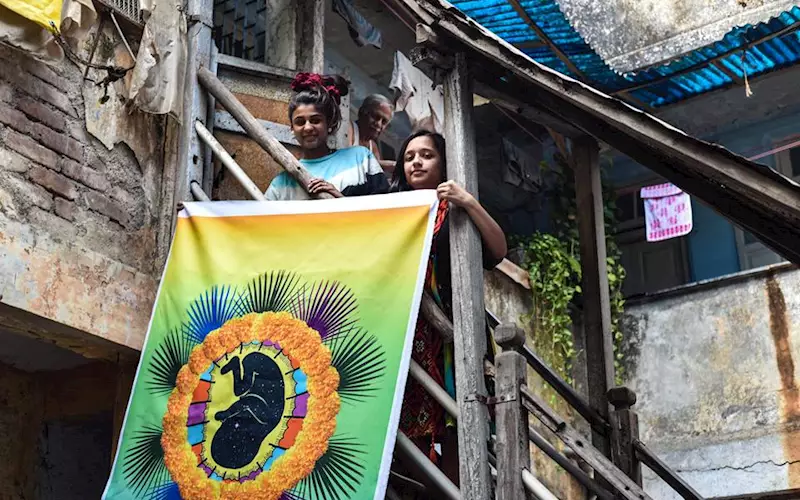
Then comes the whole process of creating the final artwork which involves a lot of back and forth in terms of style and minor arrangements
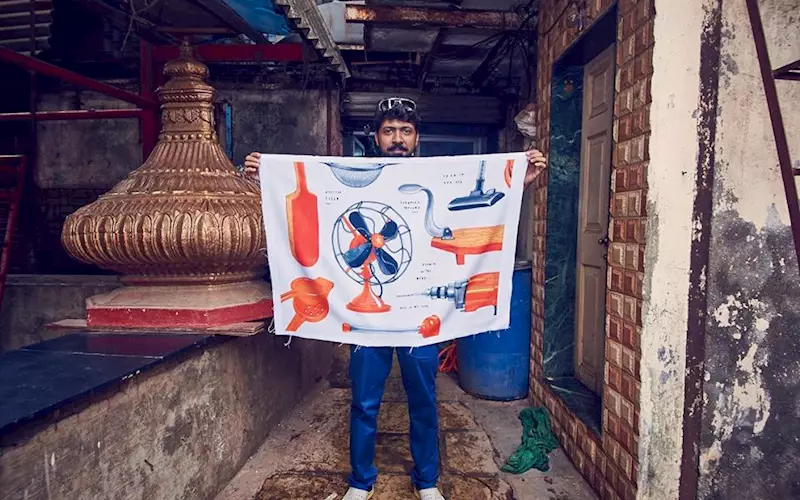
“For me, that is actually curation - developing along and giving the designer the taste of what is it like to work with another designer and another medium,” says Avlani
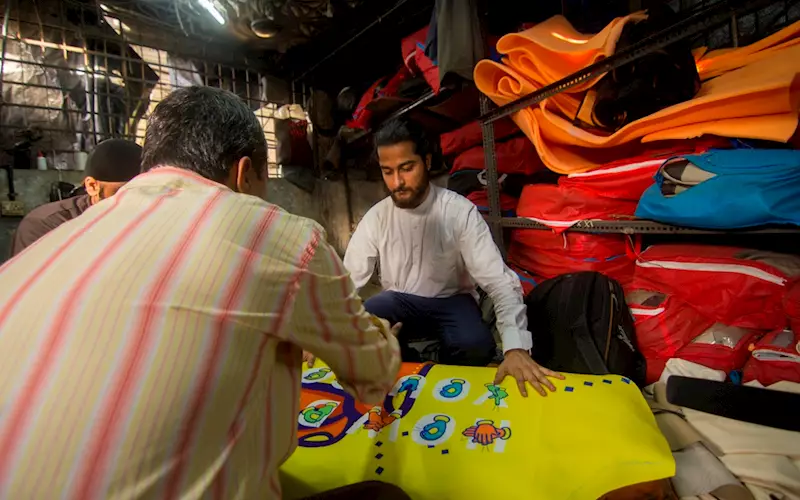
At this stage, the Taxi Fabric team also advises the designer on little but important details like how the design should be placed keeping the corners and edges of the taxi seats in mind
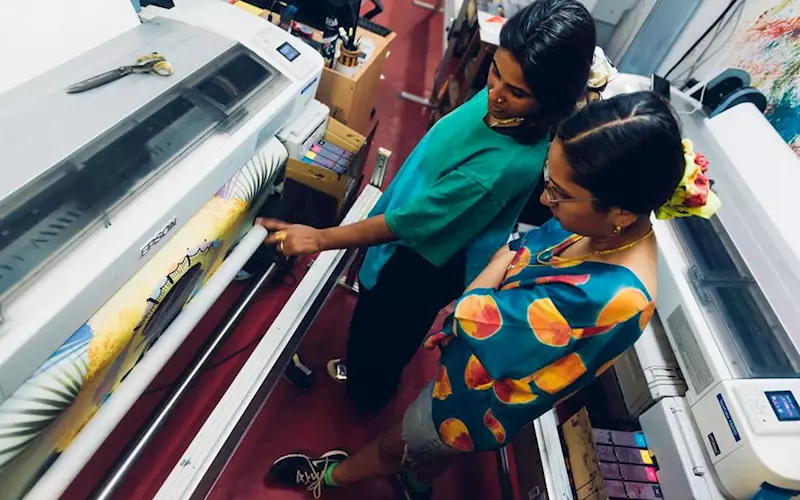
This whole process of arriving at the final design averagely takes about a month. “During this whole process, we constantly require a very high level of initiative and enthusiasm from the designer,” says Avlani
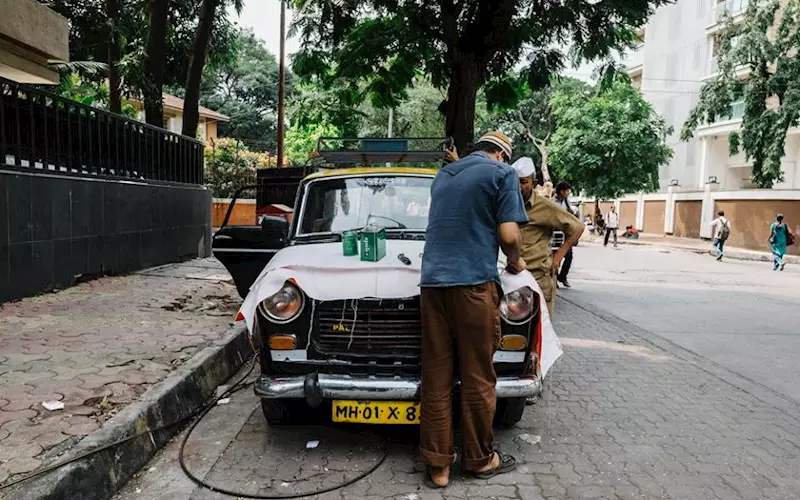
The taxis chosen for the project usually belong to friends and families of the taxi drivers that Avlani knows. An early inspiration for Taxi Fabric, in fact, is a taxi stand situated right below his house and his father’s habit of frequently taking taxis to travel
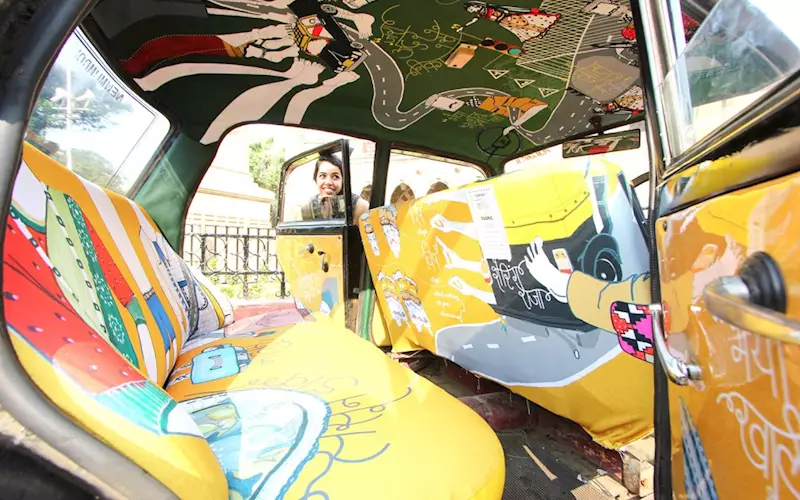
The designers ultimately get the freedom to choose the type of taxi they want to work with.” Most designers opt for fiats, which will soon be rendered defunct but are still considered the quintessential icons of the city
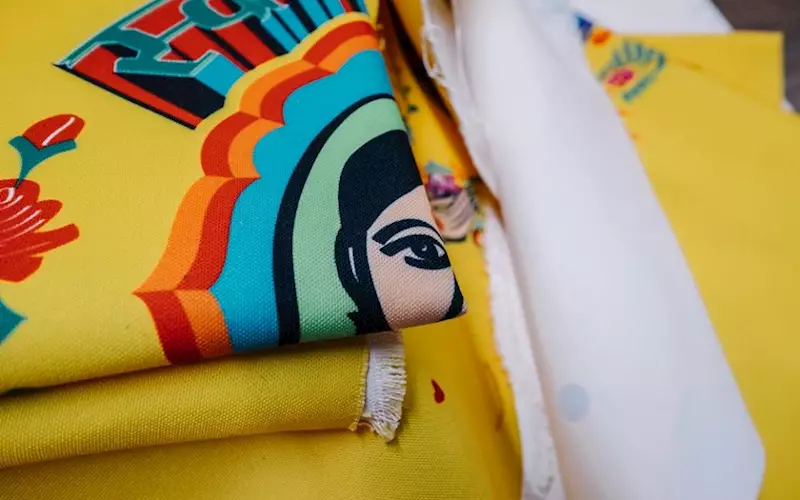
When the production process starts, Mahak Malik comes into the picture. She is Avlani’s friend and his other half at Taxi Fabric
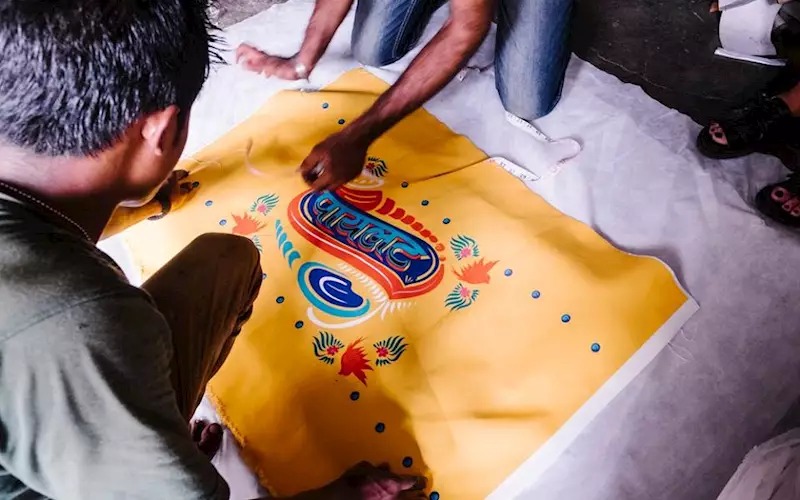
“She is the heart of the project. She takes over when we are done with the artwork. Among many other things, she creates a liaison between drivers, vendors, designers etc.,” Avlani says
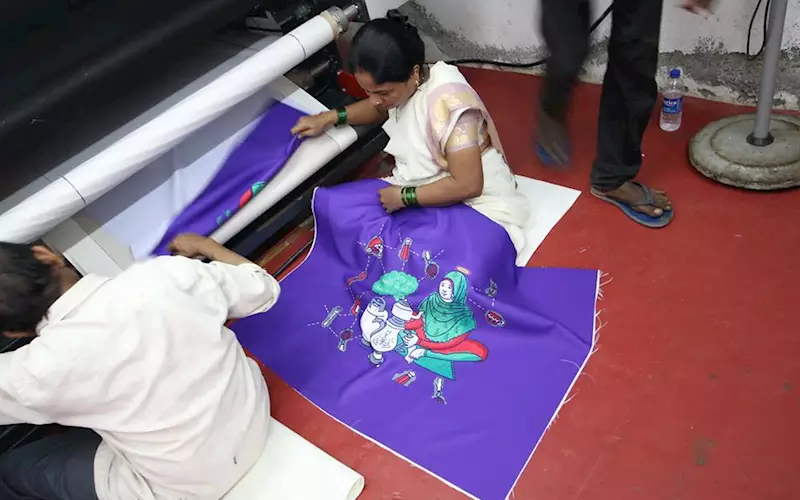
The vendors including printer Shyam Mahindrakar and workshop seat vendor Ravpreet Bhasin also enter at this stage. Talking about Mahindrakar especially, Avlani says that he has really added a lot of value to the project
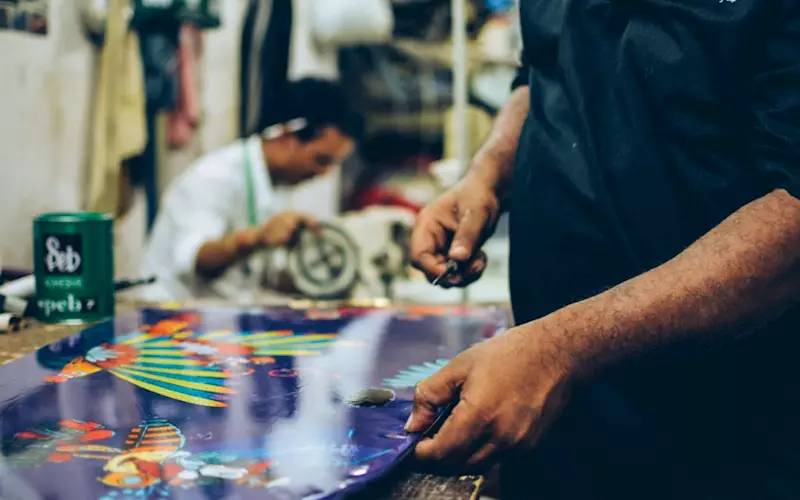
“He has an ever growing set up and he himself has shifted from technique to technique,” Avlani says about Mahindrakar
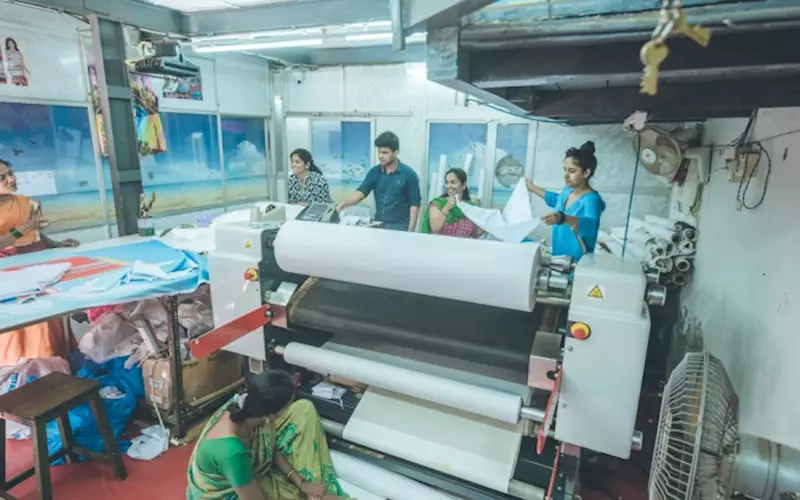
Post the final artwork, the Taxi Fabric team fixes a schedule for production which starts off with printing

The designer is present during the entire production process, and sometimes there are changes in the design even on the day of printing
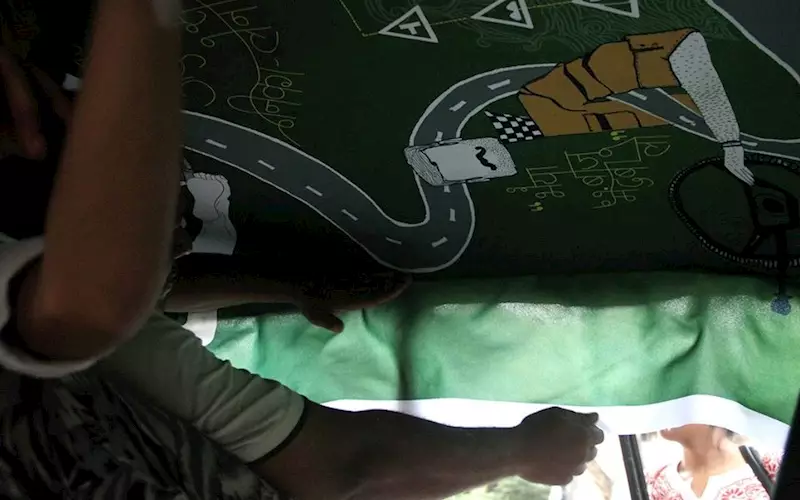
They then do colour matching, and reprint if required. On the go, they also experiment with materials
Now after many experiments and mistakes, their ceiling material is different from that of the seat and the door. The ceiling has a coat that’s water and dust proof, and there is a thin removable plastic cover on it
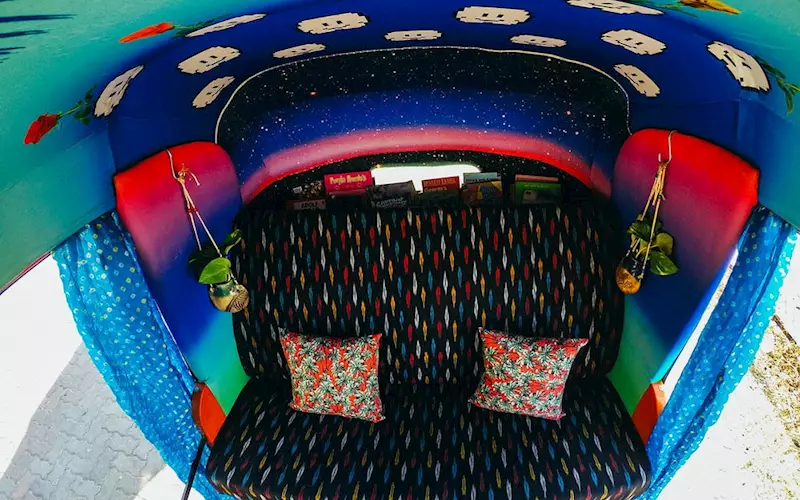
For the seat cover material, they use polyester but they keep experimenting with different GSM's and weaves in that as well
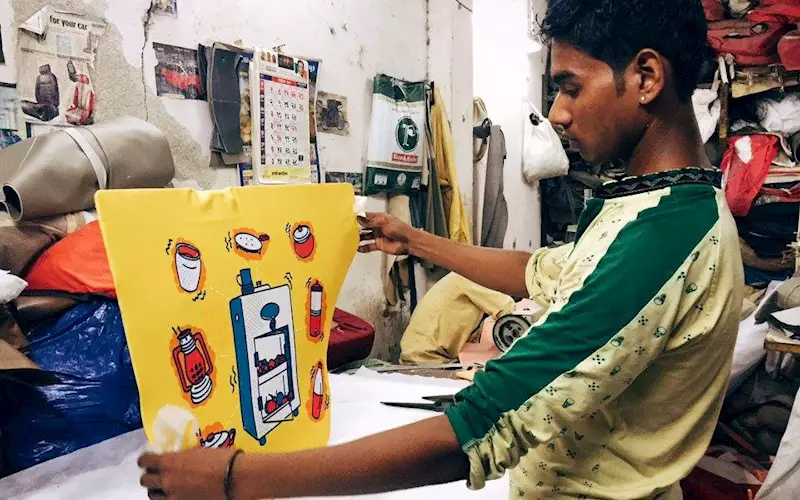
They use the process of sublimation, done through heat transfer, for printing. They first print on transfer paper on a regular Epson printer, and the design is then pressed onto the fabric
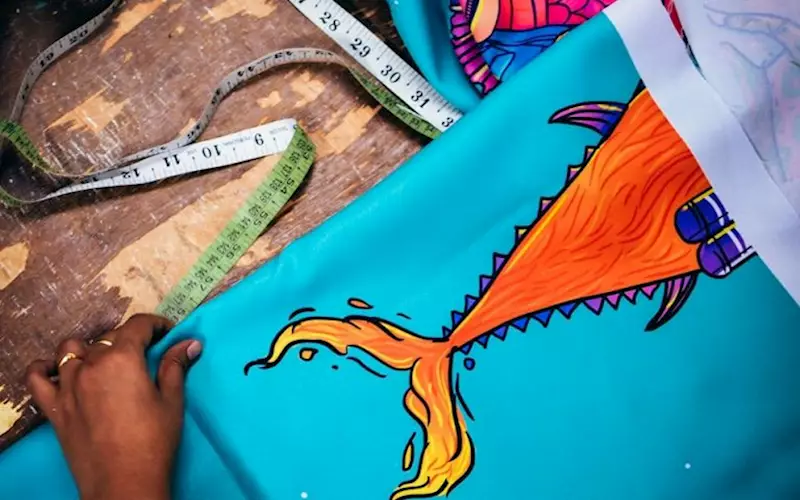
One of the challenges of this technique though includes shrinking of the fabric and bleeding of design, but now with a specific quality of polyester, that problem is being taken care of
The day after printing is marked for the fitting of the new upholstery onto the vehicle
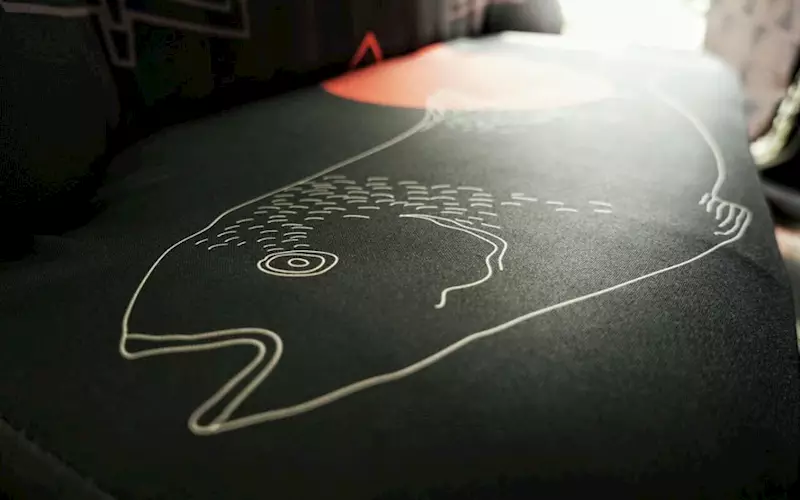
The placements are done at Bhasin’s workshop in Khar in the presence of the designer and some members of the Taxi Fabric team
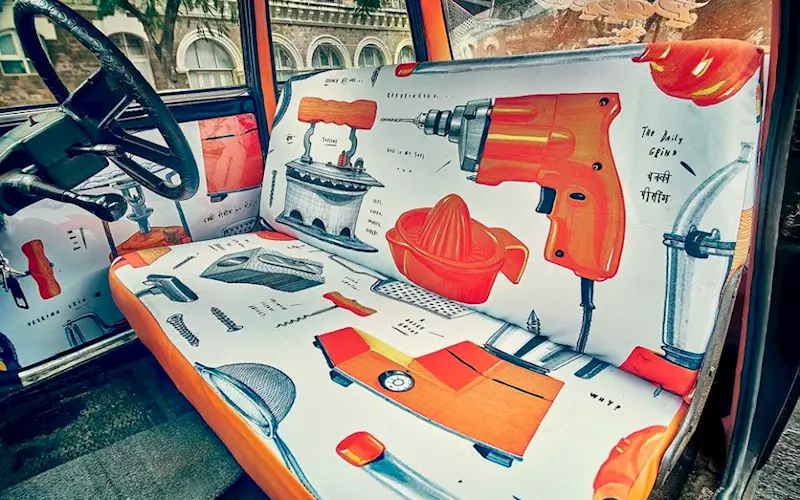
“We tell our designers to be very forgiving when it comes to the final placement as things might move a little. They need to embrace the medium,” says Avlani
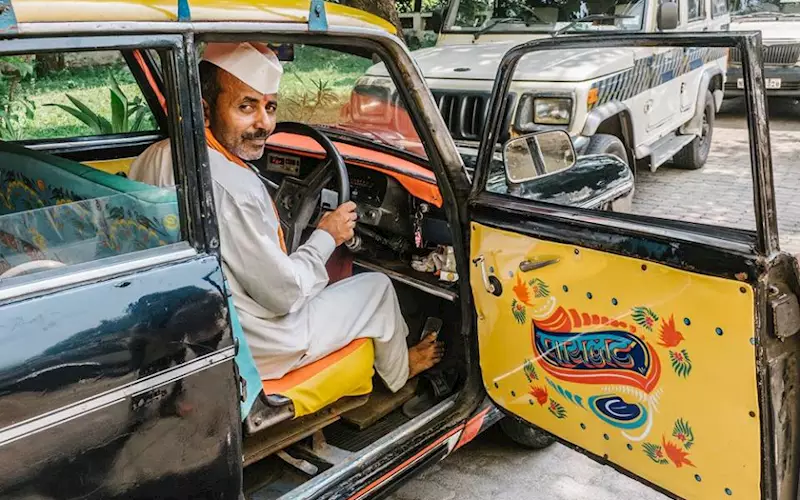
Post the fitting, the next day is kept for shooting of the revamped taxi, and then for eventually laminating the taxi