Chemco ventures into flexible packaging; adds Reifenhauser Evolution
Mumbai-based Chemco Group, a manufacturer of high-grade plastic preforms, bottles and containers, has ventured into manufacturing of shrink film as it commissioned a multilayer blown film line from Reifenhauser.
29 Jul 2016 | By Rushikesh Aravkar
The Reifenhauser Evolution line, which is capable of producing film up to 2,600 mm width, was installed at Chemco’s Vadodara plant in April 2016. It produces 14-16 tonnes of shrink film daily.
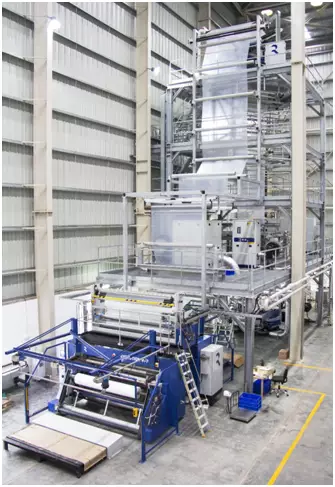
This 2.5 million Euros (approximately Rs 18.49 crores) worth investment of Chemco is in line with the current packaging trend of using shrink wrapping as an alternative to corrugated shippers and eventually save costs for tertiary packaging.
A packaging technologist informed PrintWeek India that shrink wrapping is more cost-effective than corrugated cartons as it saves more than 60% of packaging material, plus the operation can be automated thus improving efficiency levels.
Vaibhav Ram Saraogi, managing director at Chemco Group, said, “Cost and reliability being the major selection criteria, Chemco now provides ideal solutions for both primary and secondary packaging.”
Some packaging developers consider this reduction in the material requirement to be more environmentally friendly as whatever packaging material is consumed is 100% recyclable.
“We are poised to supply tailor-made shrink films. The extruders and the flow channels of the die design are devised to suit this application. Thus we can customise the film properties as per client-specific film shrinkage values in the machine direction and transverse direction, and tensile and dart properties so as to hold the package tight and withstand the abuses in the transit.”
The highlights of the Chemco’s shrink film production are: highly automated process with calibrated sensors and minimal human intervention to ensure higher degrees of consistency; the proprietary recipe used to manufacture the film coupled with imported, virgin raw materials to produce collation shrink films gives the final product “a superior combination of stiffness, strength, shrink ability and high holding force”; a well-equipped laboratory controls all aspects of quality for each and every roll ensuring zero downtime and improved line efficiency for customers.
“The USP is achieving lower gauge and better transparency and higher strength,” added Saraogi.
Established in 1980, as a manufacturer of baby feeding bottles with few injection and single-stage moulding machines, Chemco, today, has factory space of over 1,00,000 sq/m spread across10 locations in Mumbai, Silvassa, Daman, Vadodara, Bahrain, and UAE. It has 1,225 products and employs a workforce of more than 1,000.
Its marquee clientele includes big brands like Coca-Cola, Reckitt Benckiser, Bisleri, Dabur, Johnson & Johnson, Nestle, Glenmark and Marico among others.
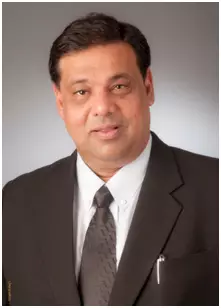
The company is helmed by the founder, promoter and chief managing director, RamawatarSaraogi, who holds an MS degree in plastic engineering and several patents credited to his name. The two sons, Gaurav Ram Saraogi and Vaibhav Ram Saraogi, handle day-to-day business operations of the group.
Chemco has deployed over 150 machines including Husky, Krauss Maffei, Nissei ASB, Dr Boy, Automa, Ferromatik Milacron, Fong Kee and Reifenhauser among others.
Speaking of future expansion plans, Saraogi said, “Various expansion projects are in the pipeline including new facilities in India,U.A.E. and Bahrain. These expansion projects will not only increase the current capacity of exsisting products but add new products like the SafeGuard envelopes targeted towards the e-commerce industry which is set to boom in India.